Iniziamo il percorso di approfondimento tecnico nel mondo della stampa flessografica su cartone ondulato partendo da un’analisi degli inchiostri e dei sistemi di inchiostrazione grazie al prezioso contributo di Davide Rastelli, Gianni Amendola e Simone Bonaria
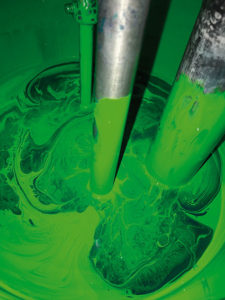
All’inizio del viaggio all’interno della stampa flessografica dell’industria del cartone ondulato, troviamo l’inchiostro, componente che, in modi diversi, interagirà con tutti gli altri componenti del sistema di stampa flexo.
In particolar modo, su cartone e cartoncino, l’inchiostro utilizzato è base acqua, dove quest’ultima è utilizzata come componente del veicolo di dispersione del pigmento e come solvente dell’inchiostro.
Un inchiostro all’acqua è composto tipicamente da:
- Acqua
- Resine
- Pigmento
- Additivi
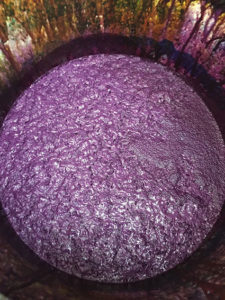
Le resine principalmente determinano le caratteristiche dell’inchiostro, adesione sul supporto, la lucentezza e le proprietà chimico fisiche.
Per poter solubilizzare una resina, di per sé insolubile in acqua, è necessaria una reazione di “saponificazione” con un’agente alcalinizzante, molto comunemente Mono Etanolo Ammina o ammoniaca; in questo modo si ottiene un sale solubile in acqua basificata.
Durante la fase di essicazione l’acqua e l’agente alcalinizzante vengono fatti evaporare con la conseguente formazione di un composto insolubile.
Dopo l’evaporazione della parte acquosa si può formare uno strato di resina morbido o uno strato duro.
Generalmente in un inchiostro non viene utilizzata una singola resina ma una miscela di resine in soluzione e di resine in emulsione.
Negli inchiostri per carta/cartone sono utilizzate prevalentemente resine acriliche in soluzione e resine acriliche in emulsione di natura dura; questo permette di avere buona stampabilità, trasferimento e velocita di essicazione.
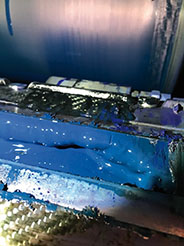
Gli additivi utilizzati negli inchiostri all’acqua posso essere: stabilizzanti, antischiuma, distendenti/livellanti e biocidi. Questi sono solitamente già presenti nella formulazione dell’inchiostro ma possono essere aggiunti in fase di stampa per migliorarne e/o aumentarne le performance specifiche.
Quando si utilizza un inchiostro all’acqua, il pH è il parametro più importante da mantenere monitorato durante tutta la fase di stampa: generalmente il valore ottimale è 8,5-9,5.
Una variazione di pH al di fuori dei valori ottimali di processo normalmente consigliati dal produttore degli inchiostri, può portare a variazioni di velocità di essicamento e di viscosità.
Solitamente il pH viene mantenuto all’interno dei valori di optimum utilizzando additivi alcalinizzanti specifici.
Un valore di pH al di sotto di quello ottimale comporta un’essicazione più veloce dell’inchiostro e una tendenza della resina a gelificare.
Al contrario, un pH al disopra di tale valore porta ad un inchiostro con una velocità di essicazione alta.
Ovviamente, essendo la diluizione effettuata con acqua, è buona cosa controllare il pH dopo avere effettuato questa operazione in quanto normalmente l’acqua utilizzata per la diluzione ha valori di pH relativamente bassi rispetto al sistema inchiostro.
Uno dei fenomeni più comuni che si può presentare durante l’utilizzo di un inchiostro ad acqua è il gelling (o impolmonimento). Questo fenomeno consiste nell’addensamento dell’inchiostro, che iniziando solitamente in racla camera, impedisce il corretto flusso dell’inchiostrazione, andando così a creare problemi sulla stampa.
Questo è strettamente legato a un pH dell’inchiostro troppo basso per cui si ha la tendenza a riportare le resine allo stato solido venendosi a ridurre nel sistema la concentrazione degli agenti basificanti. Un altro parametro importante da gestire durante la fase di stampa è la viscosità dell’inchiostro. Un valore medio per la viscosità è tra 20 e 25 secondi, coppa Ford#4. Il funzionamento della coppa Ford è molto semplice: basta versare l’inchiostro nella coppa e misurare con un cronometro il tempo che il liquido impiega a scorrere attraverso l’orifizio fino alla prima interruzione del fluido. Inoltre, essendo gli agenti basificanti sostanze parzialmente e/o totalmente volatili, è importante effettuare un sistematico controllo del pH durante la stampa ed eventualmente ripristinare il pH basico tramite l’ulteriore aggiunta di appositi additivi atti a prevenire reazioni di precipitazione e/o gelling delle resine costituenti il veicolo.
Un altro fenomeno comune durante l’utilizzo di inchiostri all’acqua è quello della formazione di schiuma, la quale non solo abbassa il livello di qualità di stampa, ma, seccando su anilox e clichè, forma una patina di inchiostro non risolubile.
Questo può essere prevenuto chimicamente con l’aggiunta di additivi antischiuma, che non devono essere utilizzati oltre la quantità indicata specificatamente per non incappare in altri problemi di stampa (pinholing); o andando a calibrare correttamente il sistema inchiostrante.
Dopo il fermo macchina si raccomanda di pulire subito accuratamente le parti venute a contatto con l’inchiostro dato che l’inchiostro secco si ridiscioglie con difficoltà, azionando il sistema di lavaggio della macchina da stampa, o se questa ne è sprovvista, andando a effettuare un lavaggio manuale, tramite il circuito d’inchiostrazione, mettendo un secchio di acqua pulita in circolazione.
È importante che non si formino residui solidi nel circuito stampa poiché sarebbero difficilmente asportabili, e inoltre potrebbero danneggiare gli altri componenti del sistema.
IL SISTEMA DI INCHIOSTRAZIONE
Altro elemento fondamentale, del processo di stampa flessografico, è il sistema d’inchiostrazione e lavaggio. Il suo importante compito è di trasferire l’inchiostro dal secchio alla racla camera/rullo gommato e di lavare il circuito prima di ogni cambio colore.
I diversi sistemi d’inchiostrazioni sul mercato, si distinguono tra loro per diversi aspetti.
Entrando nel merito delle tipologie di sistemi di inchiostrazione, possiamo dire che ci sono differenze fondamentali tra il sistema in pompa singola e quello in doppia pompa.
Fintanto che le macchine stampano a velocità relativamente basse, tutto è di facile gestione, ma all’aumento della velocità si palesano le problematiche. Sicuramente da un punto di vista tecnologico il sistema doppia pompa è più avanzato per la possibilità di regolazioni e ottimizzazioni, ma ambedue presentano punti di forza e criticità, e talvolta i costruttori preferiscono un sistema basico ma di semplice gestione piuttosto che uno più complesso ma che richiede un investimento tecnologico maggiore.
Attualmente le più utilizzate sono le pompe pneumatiche a membrana, sia per il minor costo iniziale che per le maggiori possibilità di gestione, che spesso avviene tramite un regolatore di pressione che regola direttamente la velocità della pompa. Per la manutenzione questa tipologia di pompa richiede tempo per lo smontaggio e sostituzione delle sfere interne e delle guarnizioni, causando inevitabilmente un fermo macchina.
Anche per questo motivo, alcuni costruttori di macchina da stampa per il cartone, hanno preferito l’utilizzo di pompe peristaltiche, che avendo come unico elemento consumabile il tubo di “mungitura” permette la sostituzione in un paio di minuti. Altri grandi vantaggi della pompa peristaltiche sono: l’accuratezza di pompaggio, il rumore ridotto, il consumo ridotto. A discapito vi è però il costo iniziale.
Le possibilità di regolazione, dipendono dal tipo di pompa scelto, e vanno da semplici regolatori manuali a sistemi avanzati, gestiti in continuo da PLC.
I semplici regolatori manuali hanno costi irrisori ma costringono gli operatori macchina a continue regolazioni, e impediscono spesso di standardizzare il processo.
I sistemi avanzati che utilizzano PLC per il controllo, hanno costi più elevati, ma garantiscono regolazioni fini e stabili nel tempo, con cicli d’inchiostrazione e lavaggio impostabili e interfacciabili con la macchina, permettendo di standardizzare interamente il processo.
I problemi più comuni e le relative cause
Il Foaming è una problematica dovuta a micro bolle che vengono incorporate nell’inchiostro e in altri liquidi pompati.
È un problema più evidente con inchiostri a base acqua, mentre quasi indifferente nel base solvente, e diventa più evidente, all’aumento della velocità macchina: normalmente raggiunge un punto critico intorno ai 300 mt/min.
Qui torniamo alle pompe: un circuito chiuso, crea meno schiume, ma serve un miglior bilanciamento del sistema, e quindi un più sofisticato impianto di gestione.
Perdite dalla camera racla
Questo è un fenomeno che può avere innumerevoli cause.
Da una errata regolazione meccanica, a problemi di fluidodinamica che si generano all’interno, fino ad arrivare a problematiche di usura lame e guarnizioni.
Contaminazione
Questa problematica si manifesta in maniera diversa a secondo del tipo di fluido utilizzato.
Inchiostri base acqua, base solvente, o UV hanno diverse problematiche di contaminazione, e diverse soluzioni.
La maggior parte delle problematiche è comunque legata a sistemi di lavaggio non idonei o male utilizzati. Il lavaggio è una fase molto importante che non deve essere sottovalutata e alla quale bisogna dedicare il giusto tempo e i giusti investimenti, per non incorrere proprio nei problemi di contaminazione.
Il recupero dell’inchiostro, può essere parte integrante di un sistema di lavaggio
Se il sistema di lavaggio è efficiente, avrà una maggiore capacità di recupero dell’inchiostro in circolo. Ma anche un impianto ottimizzato per mettere meno inchiostro possibile in circolo, è alla base di una riduzione degli sprechi.
L’argomento del risparmio acqua di lavaggio merita sicuramente un approfondimento. Sempre maggiore è l’attenzione riguardo allo smaltimento, sia per i crescenti costi sia per una maggiore sensibilità verso una vision più ecologica, dalla quale non è più possibile prescindere.
Oggi è sufficiente fare due conti per capire che a 0,50 euro il litro con le tirature sempre più brevi e i frequenti cambi colore, si possono raggiungere costi anche importanti a fine anno.
L’aiuto della tecnologia
È possibile avere sistemi di inchiostrazione che fungono anche da lavaggio, o sistemi di lavaggio dedicati che intervengo dopo che le pompe di inchiostrazione hanno recuperato tutto l’inchiostro.
Per concludere, l’obiettivo principale del sistema d’inchiostrazione e lavaggio, è inchiostrare senza problemi, recuperare la maggior quantità d’inchiostro in circolazione a ogni cambio lavoro, lavare in profondità ogni parte del circuito per permettere cambi tra colori differenti senza incorrere in problematiche ed infine permettere un’ambia gamma di regolazioni semplici ed efficaci.