To deepen how Dow faces today’s challenges we spoke with Romain Cazenave, EMEA Group Marketing Director and Peter Sandkuehler, Director Sustainability EMEA at Dow Packaging & Specialty Plastics. Three key concepts emerged: design for recyclability, collaboration along the whole value chain, implementing of mono-material/recyclable packaging solutions. We are confident that all that makes sense will happen, respecting environment and people and pursuing a meaningful way of doing innovation and business
Dow continues to focus on something it has been working on for years, designing packaging for recyclability so it can be returned to a closed loop system. Dow is committed to taking 100,000 tons of waste plastic and incorporating it into its products by 2025, but most brands packaging lines are not yet recyclable it is not an easy task to change to sustainable material and this is a real challenge because different materials have different properties.
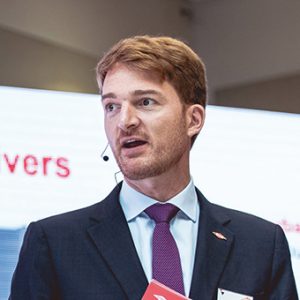
Romain Cazenave explained this idea better: “we all know that flexible packaging has many benefits, that it has a smaller carbon footprint vs rigid packaging, it is cost efficient, provides shelf appeal, protects food and prolongs its shelf life and allows for easy processability (film efficiency on packaging line, higher flexibility for customized packages). To maintain these features and propose a sustainable alternative which allows for recyclability we must develop mono-material solutions based only on one material: polyethylene. And we are actively working with the value chain to help remove more and more multi-materials structures with mono-material structures. At the moment we have a strong focus on three solutions: barrier incorporation, that is the possibility to incorporate barrier in a PE-based structure to boost shelf life and reduce food waste; PE rich thermoforming, redesigning polyamide (PA) based structure to a recyclable one according to CEFLEX guidelines; and using oriented PE technologies to provide stiffness and toughness combined with great optics as an alternative to OPET, OPA and OPP”. The first solution brings PE to really new performance levels using different high barrier mono-material structures to provide packaging with recyclability in mind. In the second high-performance PE resins enable the design of PE-rich thermoformed films, both for cast and blown processing technologies, eliminating polyamide (PA) in the structure to redesign it for recyclability.
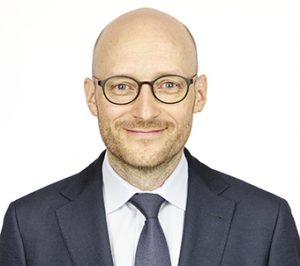
Peter Sandkuehler underlined that if products are designed with end of life in mind, nearly all the benefits of plastics can be achieved, adding that collaboration is crucial, “it’s very important to make packaging recyclable and design it for recyclability, because if we don’t do that as an industry we’ll don’t have materials to use as recycled content for future packaging, we need intense collaboration, we have to work together to achieve the result that flexible packaging will be recyclable”.
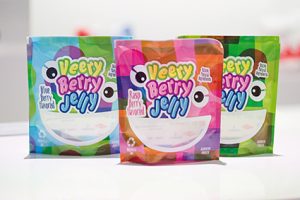
From theory to practice: a pouch can be a pouch again thanks to mechanical recycling
Dow, HP, Karlville, Cadel Deinking and Reifenhäuser showed that collaboration is the key to get real results. Obviously, said Romain, “this is just the beginning, but anyway solutions are ready and we want to collaborate even more, with our partners we can offer the best of both worlds, the efficiency of flexible packaging and recyclability, reducing the amount of materials used”. Let’s see the project in detail: at Reifenhäuser (the German group supplies tailor-made lines and components for production of high-quality blown film, cast film, sheet film, and nonwovens) were produced multibarrier films using Dow virgin resins, then the films, digitally printed on a HP 25000, were used to produce prototype pouches for food (figure 1).
These printed packages then were sent to Cadel Deinking (a Spanish recycler) to produce pellets that were incorporated in a film (PE rich structure and the recovered pellets were the 50% of total content) in Dow’s Film Innovation Center at Pack Studios Tarragona in Spain, then sent to Dow’s Pack Studios in Mozzate for lamination with a reverse printed MDO film, also produced with Dow virgin resins.
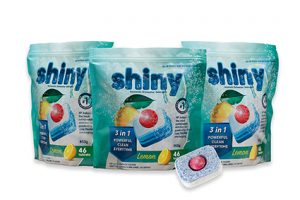
The result, a laminate containing 30% of recycled material, has been used to create new stand-up pouches to pack detergent products (figure 2), closing in this way the loop with mechanical recycling. As regards this let’s remember that Dow has developed a new family of post-consumer recycled (PCR) resins.
These recycled plastic resins are designed to harness the resources of used flexible and rigid plastic packaging to create new packaging materials while keeping waste out of the environment.
More durability with mono-material solutions
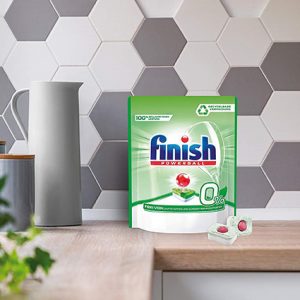
Processability with mono-materials must be guaranteed. The real stand-up pouch for the dishwasher brand Finish (figure 3), realized in collaboration with the brand owner Reckitt and Drukpol Flexo (a Polish converter), is a mono-material solution that not only enables functions such as zippers, easy opening and a good balance between flexibility and rigidity, but also, as explains Peter, “the packaging can be produced with existing equipment and this is an important prerequisite for rapid commercial implementation”.
“And this amazing result was obtained at Dow Pack Studios, the center of a network of players in the packaging technology value chain, where partners collaborate in spaces for the ideation of optimal solutions and provide the facilities to conceptualize, develop and test ideas on site in many global locations”, stated almost together Romain and Peter. Just to be more precise about the components, this re-closable pouch
designed for recyclability, offering optimal performance and consumer appeal was produced with Affinity, polyolefin plastomer and Dowlex, polyethylene resin, both by Dow.
Chemical recycling to find new value for plastics
Peter explained that for secondary packaging such as shrink film for beverages, mechanical recycling is completely sufficient. But if food conformity counts, then the chemical variant is the best option. ”Since plastics are broken down into their chemical components here, the resulting products are completely as good as new”.
Dow’s recently announced partnership with Mura Technology, a company with a ground- breaking and innovative advanced recycling technology, is a great enabler for the industry to advance the circular economy for plastics. Mura’s technology will be fundamental to close the loop on plastic waste, because it allows to recycle previously hard to recycle films and flexibles, thereby enabling to redirect plastic waste away from landfill, incineration, or worse, the natural environment. This process also helps to cut CO2 emissions – each ton of plastic processed via advanced recycling can save approximately 1.5 tons of CO2 when compared to incineration.
Another good example of this process is the partnership between Dow and Fuenix Ecogy, an innovative Dutch company that converts plastic waste to its original form, oil: through a process known as pyrolysis that breaks down polymers into oil. “Dow wants to convey to consumers the certainty that plastic packaging will be reused, but mechanical recycling has its limitations. Brand owners and consumers want to use more recyclable and renewable material in their packaging, but they don’t want to compromise on performance: chemical recycling, a process that recovers the original raw materials to be remade into high-quality resins, offers an answer”, says Peter. The collaboration foresees that Fuenix supplies Dow with feedstock made from recycled plastics, then this material will be used to produce new polymers at Dow Terneuzen facility in The Netherlands. These polymers can be used also for food packaging.
Bio-based plastics, one more time result of collaboration between companies
Dow is integrating plant based renewable naphtha – a key raw material used to develop plastics – into its slate of raw materials, creating an alternative source for plastics production. Dow is using this feedstock to produce bio-based polyethylene (PE) at its production facilities in Terneuzen and Tarragona for use in packaging applications such as food packaging to reduce food waste and satisfying the increasing global demand for renewable plastics.
To demonstrate that packaging made from this renewable feedstock can be fully recyclable, Dow collaborated with brand owner Elopak, an international supplier of paperboard-based packaging for food and beverage: Dow’s bio-based low-density polyethylene (LDPE) resins are used to coat Elopak’s liquid carton containers and in the production of carton caps, resulting in a 100% renewable beverage carton.
This was achieved without compromising the benefits of the original form of plastic- coated packaging in addition to reducing the CO2 footprint of the packaging during production and use. In this way post-consumer plastics will continue to have value for a longer period.