Redbox confirms its trust in Durst and after a P10 160 installed in 2014, last March the P5 210 printer entered the company for the creation of special applications with effects such as digital white and embossed coating, all in one single pass.
Redbox, which this year will celebrates 30 years of activity, is today a point of reference in Italy for the creation and implementation of innovative packaging solutions, POP materials, special applications and for the management of co-packing services. Activities which over the years have justified various national and international awards including that of “Champion of Growth” awarded by La Repubblica Affari&Finanza.
Numbers are of absolute importance and tell of a company that today is capable of producing 500,000 boxes a day, processing 1 million square meters of cardboard in a month.
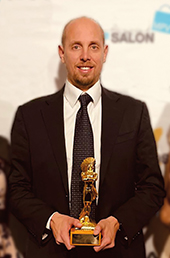
In addition to the packaging division, Redbox also has the “Creative” division dedicated to the world of displays. A team of 15 highly qualified designers operates here and develops innovative in-store marketing projects, offering customers creative ideas and cutting-edge solutions for the world of retail: POP materials ranging from displays to window signs, from promotional islands to totems and floor lamps. The complex Redbox reality also includes the Co-Packing division which offers a further but fundamental service in order to retain customers, completing the supply chain with filming, sleeving and labeling service, including also filling and packaging of the displays.
The company, although relatively young, has been the protagonist of very important growth, and today can count on a staff of around 350 people working at the production sites in Pomezia and Milan. Added to this there are partnerships abroad with local producers to guarantee time to market even across Italian border.
“Thanks to our wide offer, today we are able to follow the customer from the initial creation and design phase up to the delivery to the point of sale of the displays already filled with customers’ products, who find in Redbox a single interlocutor for all their production needs and packaging”, tells us Elena Meuti, who together with her brother Diego now manages the family business.
In Redbox, traditional and digital printing are allies in a perfect technological mix
The company, which has always been managed by the Meuti family, was born as a traditional box-manufacturing factory operating with a printing and converting process with casemakers, flexo printing machines and flatbed die-cutters. Soon, however, following the evolution of the market starting from the 2000s, it also opened to digital printing and converting technology. Today the internal production department allows us to present ourselves to the market with a vast and complete technological offer, capable of satisfying every type of need, from the prototyping of a single piece up to runs of millions of pieces, serving brands in product sectors ranging from luxury to fruit and vegetables.
Initially, digital technology was introduced to support traditional production by carrying out purely prototyping work. Management soon realized that the potential of these technologies could also be exploited for small productions, and a real digital department was therefore established.
Today there are around thirty production lines installed where traditional and digital technologies coexist synergistically, and they are also often the protagonists of projects where some components are made with traditional machines and others with digital printing.
Evidently, in this perfect workflow, technology and partnerships with the most important players on the market are one of the aspects underlying Redbox’s success. Management immediately identified Durst as the reference technological partner and the first P10 160 printer was installed in 2014. Initially Redbox used this technology for direct printing on cardboard, but subsequently its use was extended to the printing of other materials such as forex and plexiglass.
“As we have expanded digital applications on the Durst P10 printer and served extremely demanding customers in the luxury sector and mass market brands, the need has emerged to increase the speed of our production, also including special finishes in the digitally printed products”, explains Elena Meuti.
New Durst P5 210: digital white and perfect finishes for increasingly demanding markets
In an increasingly demanding production mix, where for some projects it is increasingly common to use traditional and digital systems together, the development of plastic materials, which can only be processed with digital technologies, and the growing market demand for finishing and particular effects, pushed Redbox to confirm its trust in Durst, a partner that has allowed the company to approach the digital sector, gain experience and grow so much so that it now has a separate digital production department, which has been strengthened with the installation of the new P5 210.
“Today the digital department, with the entry of the new P5 210, is able to provide much more timely responses to the market, and we are able to process very important orders in a shorter period of time than in the past,” adds Elena.
“We are very grateful to Redbox for the renewed confirmation of our ten-year collaboration and we are certain that thanks to the quality, reliability and productivity of the P5 210 configured to perfectly handle cardboard, combined with the professionalism of the Redbox team, all needs related to small and medium runs in increasingly shorter times”, comments Alberto Bassanello, Italian Sales Director of Durst Group.
Redbox’s P5 210 has a printing width of 2 meters and is configured for corrugated cardboard printing; the varnish option has also been provided which allows you to create a glossy/matt effect in relief with different thicknesses, giving the print a refined tactile and visual look. All can be done in a single step and at a very high production speed. Furthermore, the machine is equipped with white optional color, which guarantees coverage and quality, providing the company with an extra weapon to create special applications, where white is increasingly requested, and which in the past represented a weakness in digital printing.
In Redbox, which has an efficient prepress department, some options of Durst Workflow and Analytics software are also used. “We found ourselves correcting some parameters in the car, especially regarding the glossy-matt effects of the varnish. Since we are equipped with different printing technologies, our graphic designers already carry out pre-selection work beforehand and when the file arrives for printing it is practically ready for output. Based on our experience, we recognize the added value of Durst software, and I am sure that in the future, by becoming even more familiar with the tool, we will be able to exploit it further”, concludes Elena Meuti.