The demand for recyclable, paper-based packaging as a substitute for less sustainable materials is increasing. Innovation leader Sappi and digital printing leader HP Indigo have joined forces to meet the needs of a changing world. A paper-based solution from Sappi that renders additional special coatings or laminations superfluous was successfully verified for the HP Indigo digital printing.
Demand for sustainable packaging is increasing
2020 European surveys (e.g. “European Packaging Preferences 2020” by Two Sides Europe) indicate that the type of packaging is a hugely important factor with consumers at the point of sale. Paper and cardboard packaging ranks highest with consumers for sustainability attributes including being home compostable (72%), better for the environment (62%) and easier to recycle (57%). Furthermore, paper or cardboard packaging is considered to be the most recycled material, with 30% of consumers believing the European recycling rate to be over 60% (with 85% of paper and cardboard packaging actually being recycled).
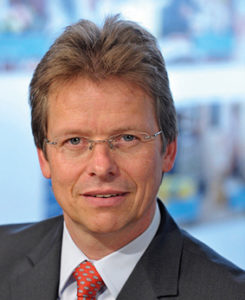
Innovation leader Sappi has been a frontrunner in the development of innovative and sustainable packaging solutions for over ten years. “With our innovative functional paper packaging solutions we are offering a sustainable material based on renewable sources that can be recycled in the paper stream,” explains René Köhler, Head of New Business Development Packaging Solutions, Division Innovation & Sustainability, at Sappi Europe. This sustainable approach also extends to the various integrated functions of Sappi’s functional papers, such as barrier properties and heat-sealability.
Elaborate production of paper-based soup pouches
To meet food manufacturers’ new demands, Sappi and HP Indigo, two experienced industry leaders, got together and put their technologies to a test. The challenge – special paper-based, sealable soup pouches – was a tricky one: Not only did each of the pouches have to be uniquely designed and personalised, but silver and invisible yellow had to be applied for brand protection as well. A material that could endure the different steps from printing to further processing by varnishing through to sealing was needed – and this, of course, always with sustainability in the foreground.
Very early on, it became clear that Sappi was ideally positioned to offer the perfect material; the innovation leader has the most extensive portfolio of sustainable packaging solutions and alternatives to fossil-based materials on the market. A decision was made in favour of Sappi’s Guard Gloss 4-OHG in a grammage of 91 g/m² for the soup pouches. “Over 80% of the high-barrier paper’s materials originate from renewable sources. The paper-based packaging solution makes additional special coatings or laminations redundant and the materials can be recycled in the paper stream,” highlights Kathrin Böhmüller, Sappi’s Sales Support Manager Consumer Goods and Self Adhesives, underscoring the paper’s perfect suitability for sustainable flexible packaging solutions such as this one.
Exploiting the advantages of digital printing
HP Indigo took over the elaborate design of the pouches. At its Graphic Experience Center in Barcelona, the 3-side-seal soup pouches (130 mm x 86 mm) were given their individual design. The team developed the artwork for the pouches and six different and unique designs, that leverage HP Indigo’s proprietary variable data printing (VDP) capabilities, came to life to meet the soups’ different vegetable flavours.
For the printing process, a narrow-web HP Indigo 6K Digital Press was deployed, using HP Indigo’s full colour range, silver and special invisible yellow inks. In combination with Sappi’s cutting-edge material, the inks give the soup pouches their high-quality appearance. The amazing results demonstrate the unique digital printing capabilities that extend from various inks to variable data and personalisation with six different SKUs.
Following the printing process, Sappi’s Guard Gloss 4-OHG excellent printability and good converting properties were improved with an additional finish: A water-based gloss coating with a high heat- and a high scratch-resistance was applied to avoid an extra lamination process. It ensures that the brilliant printing results and the excellent colour design within the pouch-making process are protected through the processing, filling and transport to the point of sale with consumers. This finish, ACTDigi Protective Coating AQ440125 by global coating specialist ACTEGA, was specially developed for the flexible-packaging market, offering a high scuff-resistance and fast drying. As the amount of coating needed is very low, it aligns with the idea of sustainability of the paper-based soup pouch because water-based coatings are environmentally friendly due to no-solvents and VOCs and they do not have a negative impact on the later recycling process.
The pouches were then finished by Bossar Packaging. The company specialises in the design and production of horizontal form-fill-seal equipment for manufacturing flexible packaging, such as spouted pouches, zippered pouches and sachets. The 3-side-seal bottom-folded pouches were produced using Bossar’s fully servo-controlled machines belonging to the BMS series. This technology substitutes the traditional and standard single cam shaft. The control is provided by means of an intuitive touch screen, facilitating format change-over and adaptability to multiple formats. This is made possible by the servo technology, which enables independent movements of machine parts.
Filling and sealing of a package are handled on the same packaging machine where filling takes place through the open-top part of the pouch. The technology guarantees outstanding efficiency as well as significant time and cost savings.
A perfect finale for a production that meets the requirements of today’s flexible-packaging solutions. With the printing, finishing and sealing processes now being adaptable to small print runs, the industry can meet the requirements of new target groups that include small and medium-sized brands, enterprises and start-ups, as well as a new generation of customers who want more individually designed packaging solutions. By using Sappi’s Guard Gloss 4-OHG, customer demand for sustainable and recyclable solutions can also be taken into consideration.