Poplast Group, a leader in flexible packaging production, will celebrate its 50th anniversary on March 17, 2025, launching a new challenge and trend in the market. The Piacenza-based company, which received the Gold Printing Award as Converter of the Year in 2024, has chosen to configure its two gravure presses with Extended Color Gamut in partnership with BOBST. We discuss this in this article and in a video interview with Carlo Callegari and Francesco Costanzo, working at Poplast Group and Alberto Vaglio Laurin, BOBST
È sicuramente un periodo d’oro quello che sta vivendo, da protagonista, Poplast Group: azienda piacentina leader nella produzione di imballaggi flessibili, con una sede anche in provincia di Pistoia dove opera la controllata FM Plastic. L’innovazione tecnologica di Poplast Group è stata premiata anche, a fine 2024, con la consegna del Premio ‘Oro della Stampa’ come ‘Converter’ dell’anno, come si legge nella motivazione della giuria, “grazie alla sua visione innovativa e i continui investimenti in tecnologie d’avanguardia. Negli anni, l’azienda ha potenziato i propri impianti e adottato processi sostenibili, dimostrando un impegno costante verso la qualità e l’efficienza. Nell’ultimo triennio, inoltre, l’azienda ha consolidato una strategia di internazionalizzazione, arrivando a una quota di export pari al 25%. Poplast dimostra dedizione per soluzioni eco-compatibili, partendo dalla stampa con l’impiego di nuove tecnologie di registro in rotocalco, l’applicazione metodica di esacromia in rotocalco ed eptacromia in flexo, e l’applicazione dei principi del design for recycling, superando la soglia del 50% di produzione con strutture mono-polimero”.
Poplast Group is undoubtedly experiencing a golden period as a key player in the sector.
The Piacenza-based company, a leader in the production of flexible packaging, also has a location in the province of Pistoia, where operates its subsidiary FM Plastic. Poplast Group’s technological innovation was recognized at the end of 2024 with the ‘Gold Printing Award’ as ‘Converter of the Year’.
This was the jury’s motivation: “thanks to its innovative vision and continuous investments in cutting-edge technologies. Over the years, the company has enhanced its facilities and adopted sustainable processes, demonstrating a constant commitment to quality and efficiency. Additionally, in the last three years, the company has consolidated an internationalization strategy, achieving an export quota of 25%.
Poplast shows dedication to eco-friendly solutions, starting with printing using new gravure registration technologies, the systematic application of hexachrome in gravure and eptachrome in flexo, and the implementation of design for recycling principles, surpassing the 50% of production with mono-polymer structures”.
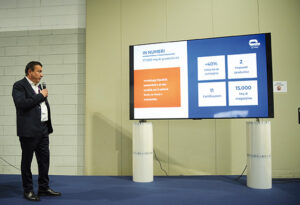
Poplast Group is a leader in the production of flexible packaging with medium and high barrier for various sectors, including food, pharmaceutical, medical, healthcare, and industrial. Sustainability for Poplast is not just a goal to pursue but a value on which to base its success. The entire product range includes recyclable alternatives based on mono-material structures in polyolefins (PP or PE), free of aluminum, certified by Cyclos and Aticelca (paper). The company’s commitment to a conscious circular economy is also reflected in its corporate ethics, with over 97% of waste recovered, the reuse of raw materials (solvent recovery plant), thermal energy, and the use of renewable energy (photovoltaic). All of this is highlighted in the second sustainability report (ESG).
50 years in the market, between tradition and innovation, looking towards the future
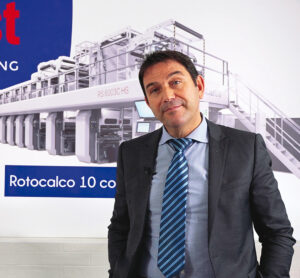
Today, the group is led by two CEOs, Carlo Callegari and Pierangelo Fantoni, along with a team of managers in key roles, including Commercial Director Andrea Ghu, Prepress Manager Francesco Costanzo, CFO Alessandro Saporoso, and Production Manager Roberto Fugazza, along with all the managers of the various production departments.
The group, founded in 1975 by Franco Corbellini and Alessandro Stragliati, followed by the entry of Pierangelo Fantoni into the shareholding in 1983, and Carlo Callegari in 2011.
It has always focused on the flexible packaging market. In 2013, the foundations were laid for growth and current results, with Carlo Callegari and Pierangelo Fantoni taking the helm and implementing an acquisition strategy (Sala Srl in 2017 and FM Plastic Srl in 2019), along with investments in technology and human resources: all this increased the group’s revenue from 24 million to 100 million euros in 2024.
Today, the two plants of the Group in Piacenza (which also houses the headquarters) and Pistoia with FM Plastic (led by CEO Fabio Firenzuoli) employ over 280 employees and cover a production area of 32,500 sm, with 15,000 sm of warehouses, 3 gravure lines, 8 flexo presses, 5 solvent-based laminators, and 6 solventless laminators (2 of which feature laser die-cutting), and 13 slitter-rewinders with complementary equipment for laser cutting and 100% inspection.
The 11 certifications, including product certifications (Cyclos for recyclability) and those related to sustainability and processes (ESG and ISCC Plus), along with an innovative and proactive prepress department, make Poplast Group a converter capable of providing significant added value to customers.
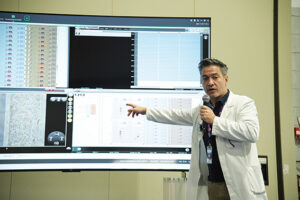
The prepress department: the heart of digitalization in gravure and flexo printing
In 2018, Poplast decided to have inhouse a prepress department to improve quality and optimize the production process, assigning the project to Francesco Maria Costanzo, a technician with extensive experience in every stage of production.
Until then, prepress merely adapted the graphic files to the technical specifications required based on characterization. With the creation of Poplast’s prepress, a completely new model was introduced: in addition to the usual verification, optimization, and color separation operations, Costanzo implemented total color management at every stage of the process, from pigment selection for inks to real-time calibration of monitors and printing machines. This innovative approach guarantees the company complete control in preventive and execution steps, ensuring superior color quality and maximum fidelity to the final result.
Costanzo and his team are the architects of a pioneering turning point that has allowed Poplast Group to replicate in gravure and flexographic printing the typical dynamics of digital printing, with enormous benefits in terms of quality, sustainability, and optimization of raw materials.
The new technology was immediately integrated into both Group’s facilities, extending the ability to print in eptachrome to all printing presses.
The high level of know-how developed has not gone unnoticed and has attracted significant interest in the industry, fostering essential partnerships with Esko and Bobst. Thanks to these collaborations, Poplast’s gravure presses are equipped with advanced registration systems featuring dual inspection cameras and inline spectrophotometers like the AVT SpectraLab XF.
Moreover, the ColorCert system performs analyses and checks that are then condensed in a report certifying the quality of all printed materials.
PopVision (Process Control System)
“During the COVID period we never stopped, but clients couldn’t be present at start-ups and had to settle for approving printed samples via photos on WhatsApp. It was disheartening to see all the preparation and calibration work for each reference going lost. What could we do?
Consequently, PopVision was born, an innovative solution that enables our clients to visualize and measure in real time what happens in the printing room comfortably from their offices, avoiding unnecessary physical movements.
This is an exclusive service from Poplast, an added value that sets us apart in the global market”, tells Costanzo. The digitalization of the process has also involved embellishment and metallic inks, improving their quality and reproducibility.
Pop7+1 (Colour Strategy)
To complement eptachrome printing, Costanzo added in 2024 a dedicated channel for metallic finishing. With this adjustment, Poplast can now not only reproduce the main reference color libraries with 7 colors but also the metallic colors, making them brighter and more uniform compared to traditional systems.
The partnership with BOBST
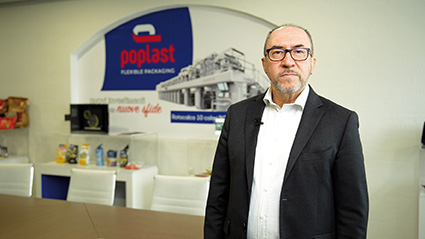
The combination between BOBST’s construction technology and Poplast Group’s innovation in printing processes has been long a virtuous case known in the market. The synergy between the two partners is the basis for a service that elevates productivity and quality to the highest levels, as confirmed by Alberto Vaglio Laurin, Business Director Southern Europe Flexible Packaging at BOBST, who has personally followed the configuration and sale of every BOBST technology that has entered production in Poplast’s flexo and gravure departments since 2016. The technical support and collaboration with BOBST’s Competence Center, led by Davide Rossello, have enabled comparative cross-testing with remarkable results: despite being in different environments and with different technical details, the color rendering has always remained perfectly aligned and performing.
Poplast Group at Ipack-Ima (Milan)
Poplast will be present as an exhibitor at Ipack-Ima (Milan, May 27-30, 2025), part of Innovation Alliance. Old and new clients will be welcomed with the entire product range of the Group and interesting examples of flexible packaging printed in 3 different subjects with the same gravure printing cylinder. The company awaits industry professionals to celebrate together its (first) 50 years of history in the flexible packaging sector. A story built on passion, expertise, and extraordinary vision for the future!