There was expectation for this open house, after the closing of the negotiations and the announcement of the sale given at the end of 2021. And the moment finally arrived in the middle of last september when soma, taking advantage of the hospitality of Masterpack, organized an open house at Veruno (Novara) plant to present the new Optima2 and the S-Mount automatic cliché mounting system
An important event that saw Masterpack as the protagonist who kindly opened the doors of its production plant in Veruno (No) to show live and operating the latest arrival, the 8-color Flexo Optima2 by Soma. The Czech manufacturer celebrates its first 30 years of activity on the flexo market placing the first flag in the Italian market, with great satisfaction of Matteo Melegatti, Area Sales Manager for Italy at Soma.
An open house that also saw the presence of several technological partners who collaborated on this project, and who during the two sessions scheduled in a single day presented their solutions adopted on the Masterpack printing machine: Grafikontrol inspection and print quality systems; Color Consulting for color management; Rossini who supplied the sleeves; BFT Group with its carbon fiber chamber-doctor blade and Praxair anilox rolls. The plates were created by Inci-Flex with MacDermid photopolymers. During the two printing demos, Enzo Consalvo, owner of Inci-Flex, explained to those present the advantages of the engraving systems adopted by the Campania service able to raise maximum print quality of a flexo machine such as the Optima 2.
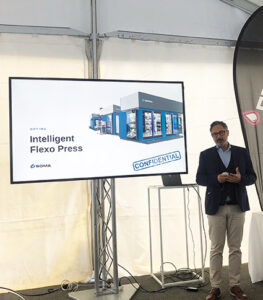
Raul Rizza, director of Masterpack plant since last July, and profound connoisseur of flexo and gravure printing technologies, had the honor of opening the short technical meeting that preceded the printing demos.
“We are happy to be the first to be able to work on this printing machine. In my work experience I have often found myself starting new machines, but I must admit that this is the first time that I am faced with a technology that, in practice, keeps its promises. Among other things, I was able to see an exceptional ease of use by our operators and I was surprised to notice the absence of a push-button panel on the machine to adjust the pressures, which are managed completely independently by the software and without the intervention of the operator”.
The Optima2 by Masterpack in detail
“What characterizes this latest generation of Optima2 is the focus on print quality”, tells us Matteo Melegatti, young but traditionally grown up on bread and flexo, for which this first installation represents a first step for the growth of the Czech manufacturer in our competitive domestic market. “The new generation of Optima2 in addition to maintaining an important solidity in the mechanical structure that guarantees absence of vibrations, is equipped with a system called Intelligent Job Tuning, which thanks to a special algorithm, it calibrates each single motor of the printing units, according to the dynamic properties of what has actually been mounted, in order to maximize the register and therefore the print quality”. It is important to underline that Soma, in its new factory in the Czech Republic, boasts a modern and equipped mechanical workshop, since traditionally, all the components considered strategic for its printing and converting machines, are made internally, to guarantee the highest quality.
The 8-color Optima2 installed in Masterpack is ideal for medium and short runs, equipped with any automatism aimed at minimizing start-ups and material waste, such as the IRIS, the intelligent (automatic) register and impression setting.
The Optima2 in general can print in wide web both on plastic films and on paper substrates with water-based, solvent, UV and UV LED inks for a maximum speed of 600 meters per minute.
Finally, thanks to the presence of S-Cloud, the computer system designed by Soma to interconnect SOMA equipment and receive assistance from SOMA service team, the operation and support is much more efficient.
Face to face with Max Binda, sales and marketing director at Masterpack
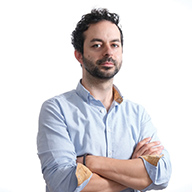
A few months after the installation of the new Optima2, what is the aspect that thrilled you most?
“The feedback I have from the printing department is that this new machine is simple and intuitive to use, and this aspect greatly facilitates and speeds up the set-up of new jobs. another very appreciated detail is that the promised print speeds, which are very important for our working approach, are actually achieved without renouncing to quality”.
What kind of jobs is the new printing machine mainly used for?
“Especially for medium-low runs, because, as previously mentioned, the combination of a very dynamic and fast machine in job changes and the printing speeds that we can achieve allow us to be competitive for this range of print runs, today requested more and more”.
You have always been a point of reference for innovative packaging solutions. What direction is the market taking?
“After the bubble of requests for compostable materials of the past few years, the market seems to be returning to the steps of “classic” plastic films but with an eye towards mono-materials, this in order to remain consistent with the” becoming sustainable “movement that was born in recent years and which is still a fundamental theme. I must also say that we are finally seeing a return in requests for materials with integrated reclosure systems, our specialty. I say finally because they are very useful solutions against food waste and I believe that to this issue, which is closely linked to the environment, is not yet given much importance. For Masterpack I also see 2023 as the year of heat-sealing paper, given the numerous requests and new projects that we continue to receive”.
How must a printer-converter present itself on the market today to satisfy the requests for innovation and sustainability coming from customers?
“The current market is very fierce and with very low prices aimed at trying to bring home as much turnover as possible. Today, in order not to enter this loop of continuous lowering of prices with consequent reduction in margins, it is essential to differentiate oneself on the packaging market, and above all by bringing customers innovations; inevitable are those aimed at bringing alternative\recyclable materials.
In our case, our research and development department, managed by my brother Valerio, is a fundamental part of our company where are developed most of the products that has made Masterpack known at European level and beyond, having started to ship regularly to North America too”.