2024 will see Markplate® definitively launch the system for marking flexo plates, and thanks to Esagrafica, representing Andrea Zanatto‘s company in Italy, some negotiations will be defined to install the solution at important flexo printers. The final solution will be ready by the middle of the year 2024
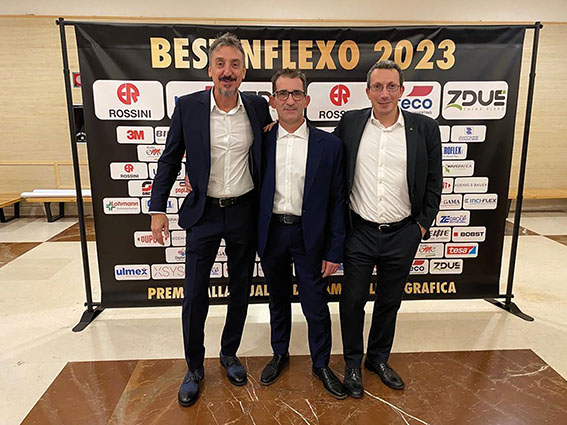
Andrea Zanatto, creator and soul of Markplate® start-up, in the last months of 2023 together with his partner Esagrafica, launched a solution, on which he had been working for at least 3 years, and considering first reactions from professionals, the solution will be able to improve the management of flexo plates for both prepress and printing companies.
The first presentation took place at the end of October in Digital Flex, which was the first company to trust this system and used it in beta tests. The solution allows the marking of photopolymer plates with a QR-Code printed on the plate, readable by a normal reader or a smartphone. This unique code does not affect the thickness of the photopolymer, does not damage the surface, does not take up useful printing area, is always readable even after countless printing and washing cycles and above all for the first time ever it is also applicable to the existing plate archive in the company.
“We thank Digital Flex for giving us the opportunity to test this technology in their workflow, and we believe it is a solution that can be used both by cliché producers but even more by printers. The Markplate® system, in addition to marking, offers a data sharing system that connects the cliché manufacturer and the printer in a completely new way. Thanks to markplate.com platform, the cliché manufacturer can share all the technical information relating to a job, and the printer can, for example, share the production parameters of a print test. The key to access the data is printed directly on the plate”, underline Francesco Felisi and Davide Bellini of Esagrafica
Marking plates and making data accessible and usable for production needs
Francesco Felisi and Davide Bellini, Esagrafica owners, helped Zanatto in the commercial launch on the Italian flexographic market. They immediately understood the enormous potential of a system that obviously does not stop at the simple marking of the plate which is initially useful for the management of logistics and plates warehouse, but through that simple QR-Code printed on the back and on the plate, a whole series of information can be retrieved that until now no one had ever considered or had ever managed to link to the physical plate.
In fact, the system foresees, in addition to the plate marker, a cloud platform for entering and sharing data, as mentioned previously. The proprietary platform is called markplate.com, here it is possible to enter all the information relating to a job. The system generates a unique key for each plate and creates a printable report. By simply reading the report, the data is sent to the marker which can be installed both by those producing the plates and by the printer, making the system very flexible.
Markplate® marker receives the data and imprints the code both on new plates and on those in the archive, allowing to mark even vast archives of clichés.
The patented marking system allows you to never have to turn the plate, minimizing the risk of damage and its unique design allows the processing of plates of any size and thickness. The control interface is completely touch and can be used and controlled remotely responding to all 4.0 features.
“When we link production data to marking, the potential of the system expands towards infinite horizons. Each printer with whom we have delved into the description of our system has brought out very interesting development points and we have understood that in addition to the key points we have identified, there are many others that can also emerge from single needs”, says Andrea Zanatto.
The first advantage that certainly characterizes Markplate® concerns logistics and management of plates warehouse. Thanks to the universal coding it is possible to use the Markplate® code also coming from different cliché producers and integrate it with the management systems already in use or adopt the Markplate® Manager management system to manage the plates warehouse and search, for example, the colors in common of a given job.
A second very important aspect is being able to predict plates wear. By using the Markplate® code and inserting it into your production process you will be able to provide valuable information to the printer on how many meters each single plate has printed. In fact, it is known that for long runs, even two or three sets of plates are produced which are replaced only when they degrade. In this case it will be possible to avoid machine downtime, anticipating replacement and avoiding waste of time and material. With a simple click it is also possible to request a remake from the plate manufacturer without the possibility of error.
In addition to data, Markplate® allows you to attach several files during encoding without any format limitation. It will therefore be possible, for example, to recall the technical files useful for the plate mounter, such as DXF, PDF or XML at the exact moment of pre-mounting.
“We have noticed from conversations with printers equipped with the latest generation of automatic plate mounters that the plate mounter is not able to obtain all the information useful for mounting. This information must in fact be entered manually into the plate mounter by the operator. All this can be avoided with a simple click of a normal 2D barcode reader. The same problem also applies to the setting of printing machines and by scanning the QR-Code present on the plate, the operator can recall and view all the parameters linked to anilox, inks, viscosity, speed, double-sided adhesive, and therefore speed up start-up and production”, adds Zanatto.
It is therefore a question of setting in motion a virtuous circle and exchange of information between printing and pre-press company, starting from the fingerprint thanks to which the printing machine data will be inserted into the management system which will then be returned to the printer during machine start-up phase, speeding up the production of the new job.
Finally, the system also filled a gap with regards to the traceability of the plates required by the BRCS regulation, which penalized the printers as they were unable to provide these data which instead with the Markplate® system is absolutely guaranteed and certain, coding uniquely each single plate.
The next developments of Markplate®
The evolution of this project, which is continuously and constantly updated, has already led Andrea Zanatto to expand the possibility of marking not only classic photopolymer plates but also sleeves and in the immediate future the solution will also be available for the marking of gravure cylinders.
“Given that the marking technology we have developed is specific for photopolymer plates, what can also be extended to other forms of printing or technologies such as gravure is data storage and management. The steel or copper sleeves or cylinders that are used in gravure are already tracked through RFID or engravings, therefore we are thinking of making the data sharing system compatible with these other applications or technologies”, adds Zanatto.
The potential of this system therefore seems to be infinite, but as the protagonists of this project underline, being a scalable system, it is important to insert it into the company and start with logistics management; only at a later stage, by using it on a daily basis, the most varied needs of single printers will emerge and they will be implemented within the system.
“From conversations with some printers it emerged that with this technology they will be able to significantly reduce the management costs of the pre-press phase, optimize printing start-up, reduce machine downtime, so the calculations are quickly done, and what initially it is seen as a cost, soon becomes an investment capable of paying for itself in a short time. We can’t wait to have the first responses in the field, the interest gathered is truly enormous and we are ready to take on this challenge and help Zanatto’s start-up to develop itself on the market”, concludes Davide Bellini of Esagrafica.
The appointment is therefore for the first months of the year when, thanks to Esagrafica, some important negotiations with flexo printers should materialize and finally in mid-2024, more or less close to Drupa, when the machine will be officially launched on the market.