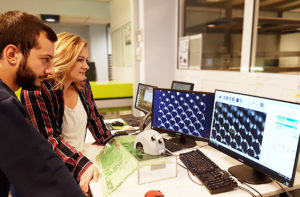
Hatzopoulos S.A. of Thessaloniki, Greece, develops and manufactures innovative flexible packaging solutions for a wide range of industries: food & beverages, cosmetics, baby food, pharmaceuticals, chemicals and agrochemicals. The company employs 380 people and, with exports accounting for more than 70 percent of total sales, is one of the fastest growing packaging producers in Europe. Hatzopoulos uses flexo and rotogravure processes and maintains business relationships with customers in more than 35 countries.
The company has been committed to innovation ever since it was founded in 1931, and during the last two years has systematically modernised its flexo platemaking and press equipment in line with the highest quality standards. Amongst other things, Hatzopoulos has invested in a new flexo CTP system for imaging photopolymer plates, a UV imaging system and a washing unit. A state-of-the art, ten-colour, central-cylinder flexo press has likewise been introduced.
In order to meet both their own and their customers’ rigorous requirements for consistently high production quality and put flexo platemaking quality control on a sound footing, Hatzopoulos decided to purchase an advanced quality control solution. The firm opted for a Sibress FlexoControl 3D Plus, a precision measuring device for analysing all key parameters of flexographic plates.
First-class measurement technology for precise and reproducible quality control
FlexoControl 3D Plus is the only flexographic measuring device in the world that simultaneously captures the surface as well as the recessed sections of dots and their base from the side. Two cameras record the surface and flanks of the dots in razor sharp resolution, so that all important plate parameters are precisely analysed and evaluated by the Versatile@flex software.
“FlexoControl 3D Plus lets us measure and document the dot percentage, screen ruling, dot diameter and dot perimeter absolutely accurately”, says Aimilia Ventouri, Flexo Prepress Supervisor at Hatzopoulos. “And because the dots are simultaneously captured from the side in the third dimension, we can also measure the plate relief and create a compatibility curve. That way, we can assess the plate’s performance compared to the curve which was used to output the artwork.”
The measurement and recording of these parameters result in very detailed control of the plate. The press-ready plates thus have everything it takes to achieve the highest possible flexo quality. Aligned with the A. Hatzopoulos S.A. philosophy for top quality in every production step, the investment in the quality measuring system from Sibress will further support the company’s continuous commitment to offering its clients around the world exceptional flexible packaging solutions.