A new investment, the second in a little over a year, and again with Nordmeccanica, confirming the positive trend for Laminati Cavanna, one of the most important Italian subcontractors specialized in the flexible packaging sector, which also thanks to new and continuous investments in high technology has managed to conquer new European customers
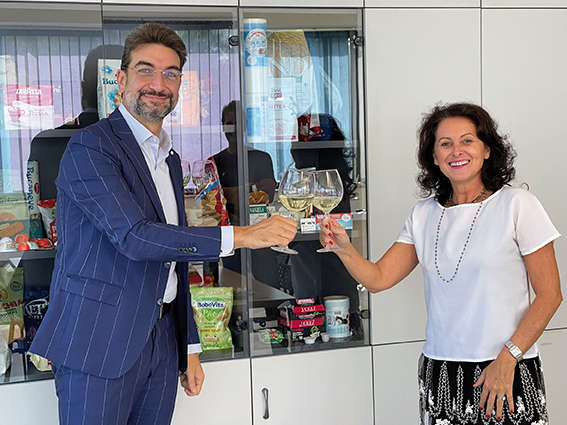
When the best of Made in Italy technology is married to the best expressions in the Italian production scene, what arises is a sparkling, not to say explosive mix, capable of enhancing that know-how, and good know-how, typical of our country. And this is what happened to Laminati Cavanna, which just one year ago announced the installation of a new Nordmeccanica Super Simplex HD laminator, and now after a few months arrived the confirmation of the purchase of a new laminator, this time model Simplex SL 1100, confirming the partnership with one of the leading manufacturers in the sector.
Important investments carried out and strongly desired by Anna Paola Cavanna, at the helm of Piacenza based company, also in light of a two-year period of strong growth, which has seen the packaging sector pass from being the main responsible for global pollution to saving the homeland when the pandemic broke out. Companies in the sector, both in terms of technology suppliers and packaging manufacturers, have shown great resilience and the ability to face new challenges with great energy and vitality. And the results were more than positive, given that packaging in the last year was the sector that recorded the best performance in the Italian industry, with a turnover of € 33 billion.
“We are in a favorable moment, with government measures that have supported industrial investments and which have therefore allowed many entrepreneurs to carry out projects to renew their technology park also to better meet the needs of a market that is now asking for recyclable and sustainable solutions”, Anna Paola Cavanna tells us in her office in Calendasco on the outskirts of Piacenza, who, however, does not hide the downside of the situation, “since the lack of raw materials is undeniable, even if the status of outsourcer puts us in a neutral position with respect to the purchase of materials, while as regards the procurement of adhesives and coatings we use in coating & laminating operations, we have protected ourselves by signing important supply contracts thanks to which we have never been without material , even if on the price side of course we also suffer daily increases that we try reasonably to let accepted by our customers”, comments Anna Paola.
Confidence in Nordmeccanica confirmed
Nordmeccanica’s new laminator, delivered last December and operational by January 2022, was the natural consequence of an increase in production volumes that had practically saturated the other machines already present in the company. “The new Simplex SL 1100 is our sixth laminator and will complete a department where two BOBST solvent-based duplex lines, one Nordmeccanica triplex solvent line and 3 Nordmeccanica solvent-free duplex lines work in two shifts. For us, being subcontractors and specialized in laminating and coating of flexible packaging, it is important to always be at the forefront of technology and offer all possible solutions; in addition to the coating of solvent-based products we are in fact able to offer coatings of products without solvent and water-based. We decided to insert a narrower web machine because we have several requests for jobs in 400-800 mm width, mainly from digital printing, which convinced us to choose this configuration. In particular, we have a client operating in the pet food sector in strong growth, so much so that with its volumes we will immediately have to commit a good part of the production capacity of the new line. We will add two new operators who will lead the company to have 57 total collaborators”, continues Dr. Cavanna, extremely satisfied with this latest investment with Nordmeccanica, which also allows for the interchangeability of operators trained at fully and same equipped training centers.
Recyclable and sustainable mono-materials and packaging solutions
The requests for sustainability of the market’s packaging are pushing converters increasingly towards recyclable single-material multilayer solutions to replace traditional structures. Laminati Cavanna in its subcontractor role acts as an intermediary between the technology supplier and the packaging manufacturer, a sort of three-way table that now brings all the stakeholders involved to collaborate to be able to find sustainable and recyclable packaging solutions. The research and development of new solutions is an area in which the Piacenza company is very active, in collaboration with the technicians of the sector. Laminati Cavanna provides its customers with machine hours and its experience to perform tests and experiments on new materials to develop new packaging solutions. “Within a European regulatory framework on recyclable packaging that is not yet clearly determined, manufacturing companies are moving on the thrust of market demands and what is established by the consortia. The “traditional” multi-material structures have been designed over time by choosing the technically best materials for the function that the packaging must perform. Polyester is the best material for printing, nylon provides excellent punch resistance and a good barrier, polyethylene provides outstanding sealing ability in all conditions and excellent slipperiness on packaging lines, polypropylene is an excellent sealer on structures subjected to thermal cycles and aluminum assures an absolute barrier to light, oxygen and humidity. The multilayer allows you to mix the characteristics of the various materials to achieve the required objectives of product protection and conservation.
The challenge is to re-design ‘acceptable’ solutions in terms of performance and cost having only one material, taking into account food safety, the characteristics of printing, laminating and packaging lines. For some products the task is feasible, while for other products which require high barrier standards and which undergo stressful thermal processes, it is particularly complex.
The alternative that the market sees beyond the recyclability of packaging is the compostable structure. The regulatory framework that governs the compostability of a package is clearer, but from a general point of view it is necessary to verify the effective ability of the composting centers to manage a high flow of non-traditional compost material. Furthermore, both due to costs and the obvious technical limitations of compostable materials, many applications are excluded from the possibility of using this type of solution”, says Anna Paola Cavanna.
The company already plans for 2022 other investments that will involve the solvent and cutting department, with the desire to always be up to date and in step with cutting-edge technologies, because today the subcontractor is no longer seen as a service provider for some production needs, but is increasingly a qualified partner with whom to develop innovative projects together.
For years, Laminati Cavanna has been ISO 9001 and BRC certified and the Code of Ethics will soon be published together with the Sustainability Report, a path that the company has decided to undertake in a completely voluntary manner, therefore with an indisputable added value. “The issues related to the environment have always been very important to us and for this reason we were the first to sign the packaging Ethical Charter becoming Ambassadors of the related Foundation in 2021. As regards the Sustainability Report, we realized that many actions were already in our daily work, it was just a matter of putting them together, measuring them, analyzing the data, and in this path we will be followed by a consultant who will lead us in 2023 to the presentation of our first balance sheet”, adds Anna Paola.
Face to face with Vincenzo Cerciello, vice president of Nordmeccanica
The partnership between Nordmeccanica and Laminati Cavanna continues…
“We are very proud to be able to continue the partnership with a highly innovative company such as Laminati Cavanna. Nordmeccanica is a leader in the production of laminating, coating and metallization systems and is, to date, the only company that can offer a range of highly technological products capable of satisfying the needs of our customers in terms of sustainability, both products and process. This is the origin of partnership synergies with our customers and, in this particular case, with the company led by Anna Paola”.
Ing. Cerciello, can you describe the new laminator purchased by Laminati Cavanna?
“The machine purchased is the SIMPLEX, laminator that has revolutionized the world of solvent-free packaging for more than 30 years. It is a machine equipped with all the new technologies in terms of tension control, mounting Siemens drivers both on unwinders and on rewinder and is managed by a latest generation Siemens TIA Portal PLC in order to control all production processes in real time. There are also two touch screens that allow immediate management of all process parameters, in full compliance with all the requirements of Industry 4.0 and the most stringent CE safety regulations. This laminator has the peculiarity of being able to laminate films of different thicknesses and different web widths in a simple way and with zero waste”.
What are the new lamination trends you are working on?
“Our company, producing the whole range of products in terms of laminating, coating and metallizers, now has the possibility to offer different solutions in line with the new requests from the customer in terms of sustainability. So, at the moment, we are working on three fronts: reducing the number of films to be laminated, replacing them with vacuum coating and lacquer processes; development of functional lacquer processes to be applied on paper in order to obtain recyclable packages; finally we are studying the possibility of having packaging in completely recyclable plastic materials. These studies are carried out always trying to maintain the barrier properties of the packaging unaltered, which has allowed us not to interrupt the food and pharmaceutical supply chains, especially during these years of pandemic”.