Originally established in 1992 as Etichettificio Salese, it was not until Marcello Busetto acquired the company in 2012 and changed its name to Labelit that the converter we see today in Santa Maria di Sala, near Venice, became one of Italy’s leading manufacturers and suppliers of labels to the wine industry
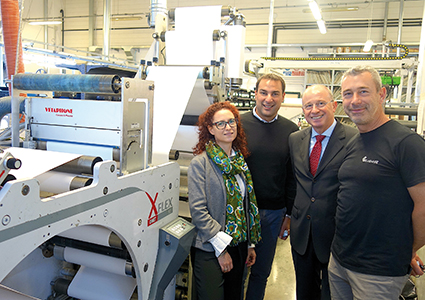
The new ownership injected a spirit of innovation and adventure into the company, as well as investment in new technology that brought higher quality and ‘added-value’ processes. “My focus has always been on improving the quality of our products, and I am constantly looking for challenges and projects that test our ability. Because we are supplying companies at the top end of their market sectors, we must meet their expectations in terms of cost and performance,” said Busetto. This applies also to the company’s choice of technology suppliers, and Labelit’s production floor is tightly packed with a variety of machines from leading manufacturers including Omet, Nilpeter and Gallus, which combine to produce an annual sales total in excess of €12m.
Being so prominent in the wine label business, where in Italy the tradition is for the more classic style paper labels, Sales Manager Letizia Gambon explained: “Output is currently split 70:30 in favour of paper to filmic substrates. But while the paper side is holding steady, we are seeing a growth in demand for film labels. Back in 2012 we were supplying labels almost exclusively to the food and personal care markets with a variety of print techniques from rotary letterpress to flexo and offset.” Today, Labelit has a spread of capabilities on web widths from 250mm up to 420mm, with a range of embellishing possibilities from foil to holograms. “This has allowed us to extend our customer portfolio and we now have a growing export business to Germany, the UK, Finland, and Turkey,” she added.
With this change in demand and the growth in filmic labels, came the need for surface treatment, and in 2015 Labelit began to investigate what the market had to offer. Marcello Busetto explained: “It became clear early on that Vetaphone was the premium brand and was the preferred supplier of both Omet and Nilpeter, whose narrow web presses we have here. When we researched Vetaphone’s history and found they were the inventors and pioneers of corona treatment, the decision was easy to make, and we have had great support from them ever since on the six systems we have here in our plant”. Most of the Vetaphone units at Labelit are the VE1A-A single-sided model, but there is a two-sided unit fitted to a Nilpeter press.
Today, a typical job at Labelit is 30,000 labels printed multi-colour with added-value finishing, but run lengths are continuing to decline. This is partly because brand owners are reducing their stockholding and relying on JIT delivery, but also because of the constant revisions to Italian legislation regarding the information to be printed on packaging. It’s a situation that Marcello Busetto does not foresee changing. “We need to be flexible and innovative to allow us to respond quickly to changes in market conditions, and we invest in the technology that allows us to do that”, he said.
One example of this was highlighted by Giuseppe Rossi, Vetaphone’s Sales Manager in Italy, who has worked closely with Labelit since the Danish manufacturer’s corona treatment technology was first introduced. “We think mostly of surface treatment being required for non-absorbent substrates like film and foil, but Labelit has been creative with the technology and by reducing the power level on its corona system has used it to clean a paper web, which gives the varnish applied a much higher gloss effect,” he concluded.