Since reliability and speed of printing are no longer limiting factors, these are now in fact driving the development of hybrid digital flexo machines. For Swiss press manufacturer Gallus Ferd. Rüesch AG it’s confirmation of the inline concept that they have always pursued. The company says that now, when developing new hybrid solutions, it builds on three phases that have shaped its digital development.
By Dieter Finna
Looking back at the design of Gallus presses, the production of labels and packaging in a single pass is in the DNA of the St. Gallen-based press manufacturer. This did not change even when electrophotographic digital printing processes and production methods with stand-alone machines made their way onto the label printing market.
The basis of current hybrid solutions
Gallus brought a hybrid digital flexographic printing system onto the market when it first entered the field of digital printing, with the Labelfire in 2016. In the years that followed, it underwent significant further development and is now used by high-performance users in 24/7 continuous operations. The demands of brand owners in the tobacco sector have significantly shaped the development of machine systems. In today’s market, the Gallus Labelfire is used equally for labels, folding cartons and special packaging. Having reached this stage, the company can look back on three development phases that it has gone through in the design of hybrid machine systems.
Phased development of digital printing
The first phase, which Gallus describes as the innovation phase of digital solutions, involves the challenge of integrating inkjet printing into a hybrid digital/flexographic printing system. The starting point for development was the initial lack of performance consistency of inkjet, compared to conventional processes. This made it necessary to integrate improved print head technology into the machine concept. With their integration, Gallus then succeeded in significantly expanding the process window in which inkjet print heads function reliably.
Due to a lack of existing solutions on the market, Heidelberg/Gallus decided in 2019 to carry out numerous in-house developments, which heralded the stabilization and thus the second phase of its hybrid digital flexographic printing system. The focus was on the camera-based “Vision System” for artifact compensation and the associated development of necessary algorithms to counteract detected errors such as missing nozzles and density unevenness in solid areas.
A major leap in print quality was also achieved by lowering the print heads nearer to the substrate, which significantly increased the jet accuracy of the ink droplets. The lowering of the heads, in turn, prompted the installation of an automatic splice detection system using sensors, in order to trigger an increase in the distance between the print heads and the substrate at short notice, when splices were detected in the web, and to protect the print heads from damage. This phase is generally referred to at Gallus as the period in which the company implemented fundamental development steps that led to stable, continuous operation of the hybrid printing systems, and ensured the company a leading position in the elimination of process errors.
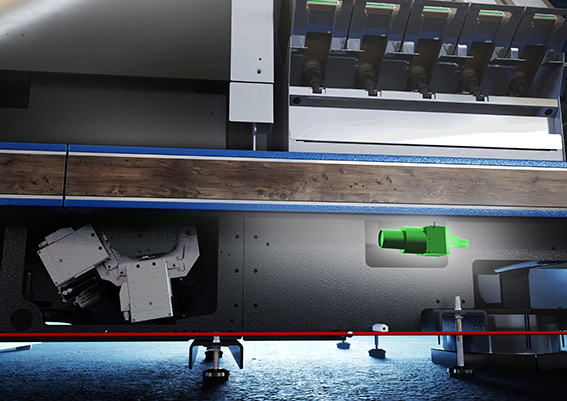
Backed by the established Labelfire technology, at the start of the third phase in 2022 Gallus focused on innovative “ease of use” concepts. Developments that simplify digital printing and take the strain off operators – an increasingly important aspect, particularly in the age of a shortage of skilled workers. This included the further development of the “Vision System” into a highly automated variant with which a test chart can be printed between each job and not just manually once a day, as is usually the case. This automated solution provides the operator with quick assistance when “weak nozzles” occur, which only become apparent during day-to-day operations. Their direct elimination affects the print quality through the greatest possible process stability and consistency.
Greater user-friendliness and standardisation are also achieved by cleaning the printheads in a fully automated cleaning process, for which the operator can additionally activate an ultrasonic cleaning step. In practice, this design solution has proven itself to such an extent that physical contact with the printheads is no longer necessary during the cleaning process, and the cleaning principle is proving to be groundbreaking for standardised cleaning of printheads.
The fixed installation of the print bars and print heads also contributes to user-friendliness. Permanently mounted printheads minimise the need for servicing and, thanks to this lower maintenance requirement, lead to significantly higher machine availability and thus an increase in productivity.
In general, all these design solutions are based on a high degree of automation with defined standards that enable the efficient integration of digital printing into hybrid machine systems.
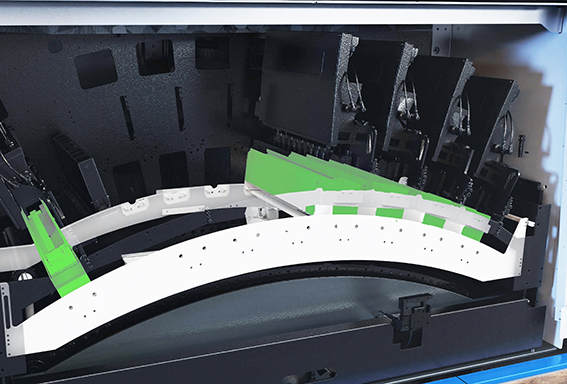
The conventional influence on hybrid printing technology
But it is not only digital printing that has gained in performance for hybrid press solutions. In parallel, the conventional basic/carrier press side has also evolved and its level of automation has increased in favour of user-friendliness. A press pre-set, for example, enables a job to be set up quickly by retrieving all press setting data from the job file. Among other things, format length and format length correction, substrate data with substrate type, web thickness and width, and web transport settings with web tension and web stretch are all pre-set.
The automation also includes longitudinal and cross register presetting, which does this for each printing unit on every job, as well as permanent register control and regulation during the run. This is a real convenience feature that frees the press operator from this otherwise constant monitoring task over the entire run.
With “web-to-web” control, sensors measure the distance between the specially designed register marks and react very precisely and quickly to deviations in the print image/register that may occur, for example, due to substrate tolerances. Since the press automatically adjusts the register as soon as the register marks are in the catching area, this mode of operation contributes significantly to avoiding and thus saving waste.
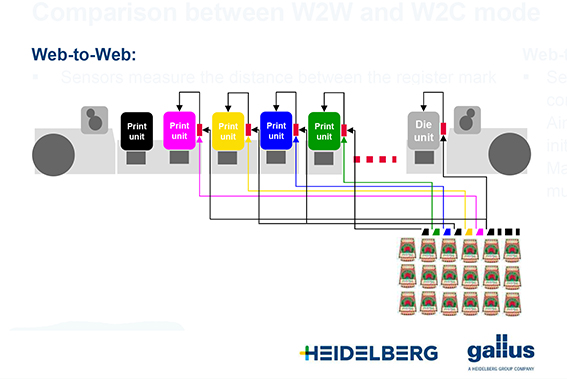
Hybrid is on the rise
If you look at the increase in performance in digital printing on the one hand and the higher degree of automation of conventional press parts on the other, this can be put together to form a coherent picture in the construction of hybrid systems. The market is currently witnessing an increase in the development of new hybrid digital flexo presses as well as digital presses with inline finishing and/or flexo units, even if various finishing processes such as screen printing, hot foil stamping, digital foiling and digital varnishing still somewhat slow down the inline process.
Depending on the order structure, the future often lies in inline operation, especially for medium to long runs and a medium degree of finishing. In this situation, it is not surprising that the Gallus One, recently presented as a stand-alone machine, also follows the hybrid DNA of the St. Gallen mechanical engineering company and contains the expansion capability to become an inline machine or hybrid digital flexographic printing machine.