The close collaboration between the SIT GROUP and GRAFIKONTROL continues in order to guarantee “high quality and zero defects” for the materials produced and used in the food packaging sector
SIT Group is one of the main gravure and flexo printers, with four production sites in which they create solutions for any need in flexible packaging.
The group is equipped with both rotogravure and flexographic printing machines followed by numerous lamination and cutting lines.
The partnership between the SIT Group and Grafikontrol started in 2016 with the design of the new San Marino factory (in which four new gravure presses were then installed) and with the purchase of new generation flexographic presses and lamination lines for the Pesaro and Stanghella (Padua) plants. To this project is added the acquisition of the Cremonese company ACM, specialized in the printing of narrow web packaging.
Grafikontrol’s choice for uncompromising quality at all stages of printing and converting
The ambitious transformation project that brought the SIT group to the highest European levels also included an investment in the latest generation technologies to ensure the highest print quality. Indeed, the SIT group had to reach quality standards such as to guarantee that the material, which will be used for packaging, would be free from any kind of defect, whether structural (in the support itself or for defects that could compromise its integrity) either for the graphic appearance of the product or information to the final customer.
In evaluating the various suppliers, Grafikontrol was chosen, because it was able to provide technologically advanced systems applicable to all manufacturing processes from printing to lamination and coating.
In this way the SIT group has unified Grafikontrol’s TQC360 ° platform. By installing 100% inspection systems on all production machines of all four plants it was possible to improve the quality control guaranteeing the uniformity of the finished product.
Grafikontrol is a company based in Milan, present on the market since 1969; for about two decades it has concentrated its activity on the study, development and production of quality control systems in the production process for the printing and converting industry. The application of Grafikontrol systems has been extended to all production sectors: printing, lamination, coating, slitting, rewinding, metallization and extrusion.
The Grafikontrol TQC360 ° modular platform
What has made Grafikontrol the protagonist and winning today is precisely the innovative TQC360 ° modular platform, developed internally, which offers customers a complete solution to guarantee quality. With TQC360°, Grafikontrol presents itself as a broad-spectrum supplier for printers and converters: products, applications, processes and services of excellence with high performance, make it, in the eyes of the customer, an “all-round supplier”. TQC360 ° products are characterized by high flexibility and adaptability to any printing process, allowing the customer to start with a configuration and implement it at any time.
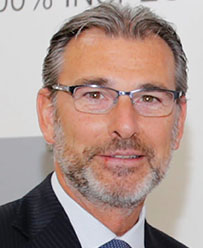
“With the SIT group we have created a tailor-made project”, states Paolo De Grandis sales director and co-owner of Grafikontrol – “on each machine, we installed a 100% inspection system on the printed side and, where necessary, the same on the back side for the control of cold-seal. The Matrix C / S dual matrix camera inspection controls have been inserted on the laminators / coaters to control the front to back register with visual and audible alarm in case the register exceeds the tolerance.
The forthcoming step is to convey all the data coming from the machines in a single Server for analysis and consultation by any authorized user, even remotely”.
Data analysis for an increasingly efficient and 4.0 production
“Having inspection systems installed on all machinery has allowed us to increase and intercept in real time all those defects that are generated in the various manufacturing processes and locate them precisely inside the rolls so they can be removed in the subsequent stage, generally on the slitters. In this way we are certain to guarantee our end customers a product free from imperfections”, says Massimo Suriano technical director of SIT Group, adding – “the supply of these new technologies, especially in our production department, gives the opportunity to our people to be more professional and to feel involved in business decisions. Our operators have favorably accepted the new systems for their simplicity because their use is through graphic and multi-touch video interfaces as in modern mobile phones or tablets, and because they immediately understood that these instruments could provide great support to their job. Grafikontrol was also very open to apply some changes to the systems, satisfying our requests, precisely to adapt them to our needs and our process routines”.
Future projects, always with a view to process automation
The projects of the SIT group for total quality control and production efficiency do not stop there and with Grafikontrol phase 2 is being planned (phase 1 has been completed equipping all machines with 100% inspection systems) which consists in connecting all inspection systems in the customer network, meeting the concept of Industry 4.0, and implementing them with an innovative and unique system on the market for tracing defects, always developed by Grafikontrol, and called Easy-Tracker.
EASY-TRACKER is the newest system for coding and tracing defects during the entire production process. The use of innovative hardware and software, entirely developed by Grafikontrol, allow an accurate removal of defects during the slitting stage. In the first process, printing or lamination, a variable code (sync-code) is printed with a high-speed INK-JET marker (up to 550 m / min) at regular intervals on the edge of the web; the sync-code contains the roll data: job number, roll number and meter length.
Whenever a defect is detected by the 100% inspection system (PROGREX PLUS / LYNEX PLUS) its position along the length of the web is immediately paired with the closest sync-code. At the end of each roll, the system generates a data-report containing all the defects detected and the related sync-codes.
The data collected by all inspection systems – relating to defects – are conveyed to a central server (NAS) which can be accessed from any location. Each roll is registered with a unique identification code which corresponds to a map of defects and can be modified by the quality control department (editing). Once digitally sanitized, the data of each single roll are stored again for use by the operators on the slitters. When a roll is mounted on the slitter for its processing, the operator downloads the relative map – an intuitive graphic document on which all detected defects are highlighted – which includes photos, dimensions, shape and position of all defects.
The position is fundamental and very important because it is necessary to be very precise in automatically stopping the slitter in the exact point relative to the defect to be eliminated: this is where Grafikontrol has undertaken to create Easy-Tracker, a system capable of precisely synchronizing the defect with the exact meter of the roll.
With this innovative system the speed and the efficiency of the whole process are increased, thanks to the automatic stops in the slitter, the elimination of defects is extremely easy.
“In addition to the SIT group, other large international groups were impressed and enthusiastic about the innovations and performances in inspection and quality control, which brought them to choose Grafikontrol as their preferred supplier”, states Paolo De Grandis.
Grafikontrol, whose motto is “Inspired by Technology”, continues to expand and improve its systems as technology makes available better hardware and more powerful software.
New solutions, currently undergoing industrial testing in their beta version with partner customers, will be presented during the most important market events.