The partnership between DuPont and 2G&P, a flexo tradeshop from Paderno Dugnano (MI), chosen by the American multinational for the final development of the top-of-the-range technology that will soon be released to the global flexo market, continues and is strengthened. A choice that fills Paolo Ghedini, the owner of 2G&P with pride. The company has always focused on high quality by relying on DuPont technologies and materials
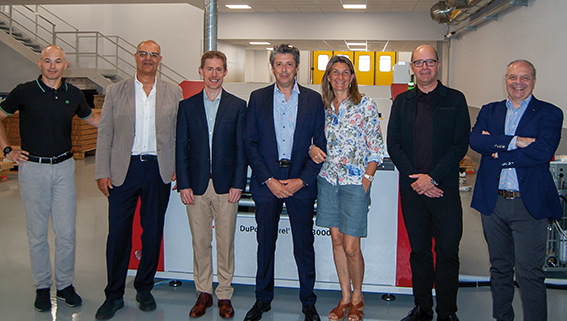
The equipment was installed in May at the new production department of 2G&P, which was chosen by DuPont as a partner for the final evaluation tests before its official commercial launch. The choice of DuPont fell on 2G&P precisely because of the peculiarities of this tradeshop, which has grown a lot in recent years in terms of size and turnover, a trend confirmed also for 2022. 2G&P always aims at offering high-quality products and service.
These characteristics have convinced DuPont to include the Milan-based service in a panel with several North American companies, which will soon test the technology for the high-volume market.
2G&P will provide DuPont with valuable feedback at this stage to optimize the performance of the new Cyrel® FAST 3000 TD. To seal the partnership with 2G&P for this world premiere, Tucker Norton Global Business General Manager Cyrel® Solutions, Jan Scharfenberg, Business Leader Cyrel® Solutions East, as well as Mario Castelli, Riccardo Labianca and Michele Negretti of DuPont Performance Specialty Products Italy S.r.l. were present.
2G&P: high quality and trust in FAST from the beginning
“Our mantra has always been to provide high quality products and services, and I have to say that the frequent double-digit growth that we record every year and the constantly increasing number of customers served, confirm that the path taken is the right one”, says Paolo Ghedini, owner of 2G&P. The success of the company has always been based on a relationship of trust with its customers, who particularly appreciate technical support and proactive attitude with total commitment to meet customer requests. This is a characteristic that Ghedini and his staff also seek and appreciate amongst their suppliers.
“Being the first in the world to be able to work with this new technology fills us with pride and satisfaction, also because I have always believed in the products and equipment of DuPont, a reality that in many years of collaboration has always followed us with care and dedication, without ever missing the necessary support. To see our commitment recognized today and to be selected for the quality of our jobs for the final tests of the latest Cyrel® FAST processor, a technology that we have adopted from the beginning, even when the market seemed to prefer other solutions and that we know deeply in every single aspect, I consider it a nice sign of esteem”, adds Ghedini.
First impressions are positive, with a uniform relief and cleaner negative elements that confirm the feeling of being in front of a higher quality plate. In the coming days 2G&P will involve some of its printer customers who have made themselves available to use the new plates for the necessary checks.
Moreover, in addition to a high increase of its production capacity, 2G&P will also be able to make an offer to the flexible wide web packaging printers interested in enjoying the benefits of a thermal plate production process by using the larger format FAST processor.
The new Cyrel® FAST 3000 TD in details
“With the Cyrel® FAST 3000 TD we complete the available sizes, the 90 x120 cm, the 106 x152 cm and now the 127 x203 cm for a thickness of up to 3.17 mm and we want to make the production of thermal sheets available to customers who require large format plates, offering them maximum flexibility. This is a clean and sustainable technology that does not provide any type of liquid: solvents, additives or water do not touch the surface of the plate, consequently the thickness of the photopolymer is guaranteed in the plant by DuPont and is not altered by the swelling process”, says Mario Castelli, DuPont Sales Manager Southern Europe and Northern Africa, confirming the continuous commitment of the American multinational to solutions that can reduce CO2 emissions and thermal development equipment goes in this direction.
“From a technological point of view we are facing a revolution compared to the past, starting from the procedure with which the plate is held inside the FAST 3000 TD, with a clamp on the head and one in the tail that guarantees perfect traction to the advantage of the dimensional stability of the plate itself. The removal of the monomer during the production process takes place using a heated roller that presses the nonwoven onto the plate which itself is supported by a compressible sleeve. This technology allows the heated roller to gently develop the plate, penetrating and cleaning out the most complex graphic elements such as barcodes. A PET film protects the heated roller, avoiding additional cleaning and maintenance steps. Another advantage is the remote connection feature with the technical assistance from DuPont’s European headquarters in Germany, which allows in case of release of a new plate or a modification to the washing program by DuPont, to carry out, by agreeing it with the customer, an update remotely, or in case of failure, to identify it and arrive at the customer with a diagnosis already made and therefore already with any spare parts.
Finally, on this FAST 3000 TD there is a catalytic oxidizer that cleans the fumes that are produced inside the machine, resulting in practically zero emissions”, adds Riccardo Labianca, Area Manager North Italy DuPont.
DuPont: continuous investments for an increasingly sustainable and quality Flexo
Although the focus of this development has been on thermal technology, DuPont will also continue to develop and support products and technologies for the solvent market, while still aiming for solutions with a reduced environmental impact. The new Cyrel® Lightning LSH plate and a new low-emission solvent have already been supplied to 2 G&P who has carried out the first production tests with satisfaction, reflect DuPont’s commitment. “We do not abandon solvent technology, so much so that we have just presented the new LSH plate for LED exposure. Cyrel® LSH photopolymer is the dedicated formulation for solvent-based development. It enables high productivity, increasing plate and print quality.
“In addition, we have introduced a new solvent, Flexosol-X, which reduces VOC emissions up to 50 percent compared to its predecessor, and 2G&P with regard to solvent plates has decided to adopt this new product, a concrete commitment to an increasingly sustainable production.
“We believe that 2G&P has all the credentials to be the perfect external evaluation partner for this new technology: great experience, knowledge of both, thermal and solvent processes, high quality production capable of enhancing the peculiarities of this equipment, which in our opinion represents the state of the art in high quality.
We already have several letters of intent for the purchase of this equipment from Italian and foreign customers, and we will be very happy to meet these requests,” Castelli adds, confirming the importance of the flexo market for DuPont and the continuous investment in R&D that will lead to the launch of new technologies and new products in the near future.
Jan Scharfenberg: evaluation of the Italian Flexo market
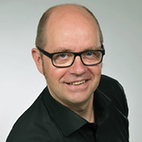
Italy is one of the strongest packaging printing markets in Europe, where rotogravure printing is still very present, but where flexography is filling the quality gap also thanks to technologies such as our Cyrel® offering, which is highly appreciated in Italy.
In addition, the Italian market is driven by a strong innovative spirit and, here, compared to other countries, there is a bigger presence of network of companies, repro-houses, printers, converters who exchange information and experiences, contributing to a quick technology development and an increased competitiveness and quality, as evidenced by the BestInFlexo awards.
I take this opportunity to thank Paolo Ghedini for the collaboration and thanks to the mutual goals, namely quality, speed and sustainability, I am sure that we’re going a long, long way together.
Tucker Norton: DuPont perspective for the future of Flexo – Solvent vs Thermal development
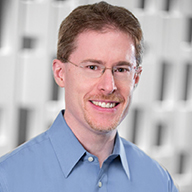
DuPont has confirmed its commitment to carry out both thermal and solvent development technologies, obviously focusing to develop solutions that have more environmental benefit. As an example, we recently published the lifecycle analysis study which showed that thermal development can represent the future for a more sustainable production.
“Although we still develop solvent technology, our future investments will go in the direction of solvent-free systems. We believe that thermal technology, which is more sustainable, has also the advantage of being extremely easy to use for the operator and requires less maintenance.
Allow me to extend a special thanks to 2G&P for the excellent relationship established. It is nice to see a reality able of making it to the headlines thanks to the quality of its work”.