DS Smith Cornuda and B+B International collaboration began years ago with the installation of Artios packaging design software, then continued with the inclusion of a Kongsberg digital plotter and now certified with Packway software.
We talk about it with Antonio Dalessandri, General Manager Ds Smith Cornuda
DS Smith has over 200 factories around the world, and the DS Smith headquarters in Cornuda (TV) is the only one of the Italian factories specialized in the production of boxes and displays.
This uniqueness in the production of American, die-cut boxes and displays allows the company to be a reference for national and multinational customers at European level. Of the total turnover developed by the company, 70% is generated by the production of conventional boxes while 30% are displays.
Among the peculiar characteristics of Cornuda plant we can appreciate the two offset printing machines. However, the company offers a wide range of products thanks to the use of different printing technologies, including flexo and digital, in some cases making use of the subcontracting transferred to other factories within the DS Smith Italia group or to third party suppliers. In fact, the strength of the Group is that all DS Smith Italia S.p.A. sites are productively and commercially complementary to customer needs.
Customers operate in various sectors and product categories, food, consumer electronics, textiles, sports shoes, large multinationals, prestigious Italian private brands and small start-ups.
Cornuda plant boasts a long-standing collaboration with B+B regarding the ArtiosCAD structural design software, a first Kongsberg X22 plotter used for sampling and a recently installed Kongsberg XP Auto plotter, complete with loading and unloading automation, used for production of small and medium runs.
The positive experience of this partnership has led to consider also the Packway management software of B + B in the choosing phase of the most suitable software.
Faced with the selection process, the reasons behind the choice in the adoption of Packway were the deep specialization for the packaging sector and its completeness, intended primarily as the ability to manage all the products that a packaging company can offer, American and die-cut boxes but also boxes composed of several elements with different raw materials and production cycles, laminated boxes, cases and above all displays.
The completeness of Packway consists in the ability to manage the entire business management process, from CRM to the production planner and data collection from the machine, to logistics, shipping, quality and directional analysis, all within a single software, therefore without the use of external technologies.
All this supported by the fact that Packway is currently used by over 200 companies in Italy, some of them known and collaborators of DS Smith Cornuda.
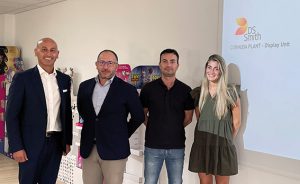
Face to face with Antonio Dalessandri, General Manager DS Smith Cornuda
When and how did the relationship between DS Smith Cornuda and B+B International begin?
“The collaboration between our factory and B+B International was born several years ago, first we included the ArtiosCAD design software, entrusted to the care of Cristian Zavarise. With it we began to draw and design boxes, following the training course provided, also at other plants of the group, to learn the techniques and criteria for designing and filing the work, evaluating how compatible they were with our working systems. From there we began to build not only the technical office but also a workflow that was as consistent as possible with our commercial proposal, in order to have information that was essential, quickly available and above all correct. We then installed the Kongsberg X22 Plotter and concentrated ourselves on display design. The inclusion of ArtiosCAD and Kongsberg technologies have accelerated project completion times by facilitating the entire commercial structure, freeing it from procedures that are no longer necessary, giving the opportunity to focus more on design, cutting and prototyping to be offered to customers”.
What were the reasons that led you to introduce Packway?
“The inclusion of CAD/CAM technologies was fundamental because it gave the possibility of having in-house design and therefore being able to design and create prototypes quickly, providing immediate answers to customers. Furthermore, having all the development internally, increases experience and knowledge, facilitating operations in the short term, giving the possibility to be much more competent in the medium to long term. We manufacture boxes and displays, but by our customers we are increasingly seen as a service company, which must solve problems and offer solutions. In this context, the collaboration of the sales department with the technical department is very important and for this reason are necessary appropriate tools and technologies.
In 2015 we installed Docupoint, the Packaway module that allows you to manage Pre-Production activities, that is CRM commercial activities, technical office management and quality. This was necessary because we realized that by strengthening the structure of the commercial and technical office, the information we had was entrusted to human memory and to a filing system that was based on the individual rationality rather than on a collective one.
For this reason we wanted to install Docupoint also mindful of the excellent experience lived by the DS Smith sites of Rosà and Vigasio. The inclusion of a new resource such as Laura Michelon has made it possible to manage the transition between old and new management with a vision not rooted in established habits.
Docupoint helped us a lot to put our workflow in order. At that point we faced, not without difficulty, the most important challenge for the plant, the inclusion of Packway management software, different from that used by all the other Italian production sites, notwithstanding with DS Smith’s corporate policies.
The difference between the factories that exclusively produce boxes and Cornuda, which also produces displays, highlighted the peculiarities and management complexities that the previous software was unable to support. There was a need for a tool capable of fully managing all our products and processes, at the same time flexible and agile in management. This led us to choose Packway, also guided by the professionalism and specificity of B+B people in understanding our needs and addressing us with the right timing and the correct support for the introduction of their management system. After a short run-in, with the help of everyone, both B+B technicians and colleagues, we entered all the data and with the right timing we understood how to use in the best way this new software. Now from a functional point of view with Packway we have connected all departments from CRM to sales, to order management and estimates, to planning, final accounting and shipping: so we managed the entire production process in detail”.
What impact did Packway’s Technical Data Sheet, Estimates and Orders features have?
“We needed a tool that would facilitate us throughout the project development process, including of course the offer to the customer. Estimation is a crucial moment for every company, especially for those who, like us, manage complex products such as displays.
B+B responded to our need with Packway and the Data Sheet functionality. In a simple screen shot it is possible to graphically view all the raw materials used and the entire production process of a product, truly considering every information. The technical data sheet was designed precisely to facilitate display manufacturers and those who need to have all the data relating to the material, equipment, production processes and special processes needed to create the finished product in a single file. With Packway, quoting has become simpler and more intuitive and has allowed us to reduce processing times for offers.
In our opinion, Packway’s strength lies in being able to manage in the same way, thanks to the tools just mentioned, both simple and complex items, and those requiring various types of raw materials and processes”.
How is production managed?
“Our production is supported by Packway Production Planner which allows us a precise and complete scheduling of orders, having also implemented the installation of the terminals on the machine. In fact, it is essential not only to plan our internal activities but also the external processes entrusted to subcontractors. Knowing the methods and times and incorporating them into our production program means having a clear situation of all stages of production and of each single order. This allows a continuous improvement in the relationship with the customer and with the suppliers, who get precise and reliable delivery times as well as giving us the possibility to plan and accept orders with the certainty of being able to fulfill them respecting the established agreements. Furthermore, the production management, through a planning and graphic visualization application, also in this case moves the knowledge from the single person to the company software, allowing more resources to have an immediate visibility of the workload and to be able to make the most appropriate considerations.
The possibility of having a complete and precise production planning through the implementation of the planner, the machine data and the logistics was another important challenge within our company, and it was fundamental from an industrial perspective, especially for growth, aimed at complex items such as displays. In our sector many companies make displays, but often in limited quantities, now our factory can produce complex items in both small and large quantities with the same simplicity”.
What were the main objectives that led you to the inclusion of Packway Logistica?
“We needed to have a unique and complete management software also for logistics, capable of managing all business processes and with Packway Logistics we were able to achieve an exceptional result. The management of the finished product and traceability were the main objectives, implementing the logistics in all phases was a fundamental action for us because we have about 4500 pallets in stock at maximum, including many references that can reach 800. The location of the material is fundamental because we follow the logic of the available space. We need to use FIFO (First In First Out) logics because very often within an order we can have the management of an item that can have, for example, two different prices because it could have been processed at different times. Furthermore, customers increasingly introduce graphic variations within the same order even during the year and this clearly further complicates the management phase, but with Packway we manage everything in a precise and rapid way.
Having the traceability of the individual pallet is a must and we aim to make it automatic using the existing labeling, with logic related to the consumption of raw materials to better manage the warehouse. This aspect has also greatly improved the monthly reporting activity. We can affirm that in these areas we have made significant improvements in recent years, thanks to Packway Logistica we are able to be much faster in analyzing and managing data, also increasing safety.
It should also be noted that the quality of people’s work has improved, the time to follow the activities has been reduced thanks to the choices made for the implementation of B+B products, certainly if we had not used them long ago, today we would have the offices clogged with bureaucratic activities more laborious than those we are doing today. This improves our workflow but above all leaves us more time to devote to the customer and his requests”.
What were the elements that led you to choose B+B as a partner for such a strategic product as management software?
“We have known B+B for over twenty years, the people who are part of it and the strategy of the company. We have identified in Packway a management software that fully meets our needs. B+B has developed this management software exclusively for companies in the sector, and it is an essential aspect of the product but also of the people, of B+B consultants who speak the paper industry language with professionalism and know the production processes of our world. This with a medium-long term perspective, so much so that our collaboration does not stop, indeed we are already thinking about the next step together with B+B.
Management software has become one of the most important strategic assets, it is the backbone of the company, through which people, technologies and processes are organized to create value for our customers and for our company”.