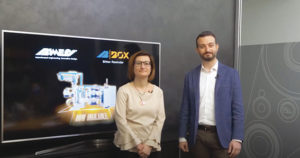
With a double digital event, one in Italian and one in English, Bimec presented the new slitter-rewinder BBox with automatic change, born from the evolution of another historical Bimec model: TCA 64E.
Elena and Davide Bottoli welcomed the virtual guests, presenting and studying the most important technical details of this new slitter-rewinder.
BBox was born from a careful analysis of market needs and aims to satisfy them thanks to the introduction of innovative solutions. “Increase in production with a request for more performing machines, increase in versatility to be able to process different materials, and an increase in flexibility with machines equipped with automatisms capable of reducing downtime at each set-up or unloading of the machine”, begins Davide Bottoli, underlining how not all the solutions present on the market are able to meet these needs, and also recalling how often some automatisms applied to the cutters are not so effective and respond to real production needs, also risking slowing down the machine in set-up and job change phases, making it even more cumbersome or less accessible in some points. Automation is necessary, but only where it is really necessary and brings the advantages for which it was designed, this was the focus of Bimec in the planning and concept of this new slitter-rewinder.
The BBox in detail
BBox is a cutter with automatic change, with separate unwinder, aerial passage of the film and winding under the bridge, with the addition of a series of fully automatic and semi-automatic technical solutions, designed and introduced with the aim of reducing unproductive times between one work cycle and another. “The objectives we want to pursue with this new machine are to make the most of the performance, equalizing the accessory and winding times thanks to a higher speed of the accessory equipment such as loading, unloading, reel closing, restarts, thanks to the addition of automatisms and operator servo-assistance”, adds Davide Bottoli, “the second objective is to introduce rapid set-ups to make the machine flexible for every type of work”, concludes Davide, moving from the analysis of the machine rendering to the production department of the new Bimec plant where the new BBox is already available for any type of test with customers’ materials.
Now let’s discover the new BBox in every phase, starting from the automatic core loader, which can house both cardboard and plastic cores from 70 to 152 mm in diameter. The next phase involves the automatic positioning of the cores, which works in two phases to ensure speed and precision. This automatism has been integrated into the ejection device and is designed to perfectly balance strength and precision.
A very important feature is the position of the operator, conceived in such a way as to be able to manage from the same point both the unloading and palletizing phase of the reels and start the closure of the reels unloading and allow the next production cycle.
During the fifth wheel change, welding and application of the double-sided tape, the attachment of the material tails for the new cycle can take place in two different ways: automatically by means of an adjustable sealing bar (obviously for all weldable materials) or manually by applying double-sided tape in a convenient position for the operator, thanks to the particular configuration of the machine.
The closing phase of the finished reels has been purposely left to the intervention of the operator, who performs the operation manually, since in this phase the needs of the customers can be very different from each other to the point of making inefficient or even counterproductive the insertion of an automatism. Just below the command and control display of the cutter, a double-sided adhesive dispenser has been placed within easy reach of the operator.
The automatic pusher with reel unloading, in addition to positioning the cores for starting the production cycle, also has the function of transferring the daughter reels from the winders to the arms of the reel unloading. In the last phase, the one that sees in action the coil unloader and the manipulator, Bimec has paid great attention to the introduction of a very versatile accessory, namely the rotating reel unloader, which allows manual unloading for lighter reels, servo-assisted unloading, controlled by the operator, for the transfer of the reels from the arms of the reel unloader to the manipulator and to the final palletizing phase, and finally the opening from 0 to 90° on vertical and horizontal axis followed by the descent to pallet level, very useful for reels of a certain size, which must be palletized without the need to be overturned.
The 0 gravity manipulator can handle reels up to 300 kg and allows the double gripping of the reels which halves unloading times; moreover, both the pushers and the manipulator arms are completely independent so as to manage the two axes separately.
“A machine with several devices that intervene in sequence or simultaneously as on the BBox must also be intuitive and user-friendly, so we decided to equip it with LED indicators, laser pointers and sensors that facilitate man-machine interaction, in particular 4 LEDs, each for each device described above, which communicate through 4 colors to identify 4 different machine states”, concludes Davide Bottoli.
The BBox, extremely compact machine, is able to process rolls of 1050-1350-1650 and 1850 mm in width with a maximum diameter of the parent roll of 1000-1200mm and a maximum diameter of the finished rolls of 610mm. The minimum cutting width is 20mm, while the machine is able to reach the maximum speed of 800 meters per minute.
Face to face with Davide Bottoli
What types of customers does BBox address?
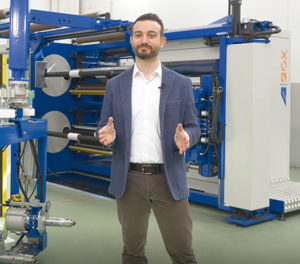
“BBOX is a slitter rewinder intended for cutting plastic films, paper and laminates and, in general, all materials used in the flexible packaging sector.
It represents the ideal solution for converters who need to have a machine with quick settings and which allows flexibility in work variations. Furthermore, BBOX has been designed to be ergonomic, compact and user-friendly: thanks to its configuration, it allows the operator to control the various operations of the machine from a single position – that of unloading – being able to dedicate himself for the most part of the time needed to pack the reels, reducing unproductive times and thus positively affecting company productivity”.
After more than a year of “Covid emergency” what is your balance?
“Although the emergency forced us to reduce the presence of employees on site to ensure collective safety, 2020 was a year with a positive balance. We have managed to meet delivery dates agreed with our customers prior to the pandemic and have acquired new ones, many of whom have already put our machines into operation with full satisfaction.
Our technical department, always in synergy with the sales department, has worked hard in engineering technical improvements on our systems to offer greater benefits to customers, with a view to optimizing and simplifying production processes”.
What actions did you have to take to ensure customer service?
“The pandemic situation forced us to drastically reduce travel and, although we already used to provide remote assistance, we decided to reorganize and improve this service. Thanks to the new digital communication tools, we are able to guarantee complete assistance to our customers, both as regards the installation and testing of our machines remotely, and for any downtime. With remote management, we are in fact able to control the functioning of Bimec systems around the world from our offices and to intervene promptly 24/7. New investments are aimed at these activities but it is still early to reveal what we are working on. However, we are confident that these innovations will provide a great advantage for the converting sector and we look forward to sharing them with our customers”.