Bobst Italia, based in San Giorgio Monferrato (Alessandria), celebrated with a great event, which took place on 2nd October 2020, the completion of an ambitious renovation that began in 2016. Carried out in three successive phases, the project has completely renovated the buildings and production organization, making the company one of the most modern production centers of BOBST
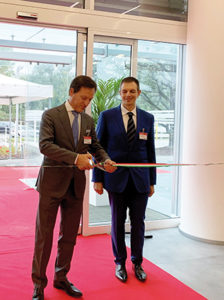
by Jean-Pascal Bobst.
On his left the CEO of Bobst Italia Davide Garavaglia
A day of celebrations on October 2nd for Bobst Italia, which inaugurated the new plant with the presence of all the employees, some important Italian customers (Cellografica Gerosa, Goglio), national, regional and local political authorities, in particular the mayors of 7 municipalities in the area, because the investment of the Swiss multinational in this area has a significant impact also from a social point of view. An investment that between headquarters and innovative technologies in the new 2400 square meter Competence Center, at the forefront for demonstrations of machines and research and development tests with a fully equipped laboratory, amounts to approximately € 20 million.
In full compliance with anti Covid-19 regulations, the event began with the symbolic cutting of the ribbon to inaugurate the site by CEO of the Group, Jean-Pascal Bobst and CEO of Bobst Italia, Davide Garavaglia,which was followed by a series of interventions by the Bobst management in front of the 400 staff and guests gathered for the occasion.
“The complete restructuring and expansion of the site are the most evident aspects, but the transformation is much deeper”, explained Davide Garavaglia.
“It has modernized the organizational production flow, logistics and traffic inside and outside the company, and improved the layout of all solutions in the shop.
It is now a state-of-the-art facility, maximizing energy and water recovery to reduce the environmental impact and optimize the working environment in terms of health and safety”.
From Rotomec to Bobst Group, 60 years spent alongside the flexible packaging industry
The San Giorgio Monferrato site has been producing machines for printing and converting flexible packaging since 1960, the year in which it was founded as Rotomec SpA. Today the production capacity, also in light of the latest investments, is about 100 machines a year.
“A part of the number 1 rotogravure press is still present and since then over 2,500 more have been built, most of which are still in operation in many parts of the world. Retracing the milestones of Bobst Italia, I don’t think I’m exaggerating if I say that this company represents an important part of the printing history in Italy and worldwide. Our suppliers were among the first to understand the enormous potential of the food packaging market, which has had and will continue to play a fundamental role in the development of contemporary society. Even in the light of recent events it is clear to everyone that without flexible packaging our modern lifestyle would not be possible. Our company is the cornerstone of this industry, because here were born and developed innovations that allowed our customers to create safe, innovative, ecological and, why not, also beautiful packaging”, said Davide Garavaglia, recalling that today BOBST is a world leader in the rotogravure printing presses sector, with a market share of 17%, far ahead of German and Chinese manufacturers.
In 1987 it passed to the Finnish group Valmet Converting, which was in turn acquired by BOBST in 2004. The acquisition was part of the strategy of the Swiss manufacturer of folding carton and corrugated cardboard packaging machines, aimed at diversifying and significantly extending activities in the sector of flexible packaging. Shortly thereafter, the site became the Group’s Center of Excellence for gravure, laminating and coating technologies.
Jean-Pascal Bobst: “The story of Bobst Italia is the story of a lasting success”
Present in the factory and acclaimed with great affection during lunch by all Bobst Italia collaborators, Jean-Pascal Bobst wanted to be present for the event, as often happens in the most important moments involving his Group’s locations around the world. Mr. Bobst recounted the moment in which the management of Bobst Italia, gathered at the Group headquarters in Switzerland, presented the business plan for the new investment, and how from 6 million initially requested, the Group finally decided to allocate 9, to these about 12 were added for the innovative technologies present in the Competence Center. This is in fact considered a strategic pole for business development in the flexible packaging sector and it is here that packaging innovations are developed, in partnership not only with printers and converters, but more and more with their customers, global multinationals, for team work that involves all the players in the supply chain. A centrality in the strategy of BOBST, which focuses on this site as a world research center for gravure printing, lamination and coating.
“It is great that the inauguration of the new location coincides with the 60th anniversary of the founding of Bobst Italia”, said Jean-Pascal Bobst. “The story of Bobst Italia is the story of a lasting success.
In 2004, when this site entered our Group, there was technology but not a strategic vision of the future, machines scattered everywhere, of different shapes and colors and a way of producing that was not in step with the standard required by the global market. Today Bobst Italia is a factory organized on the dictates of Lean Production, capable of transforming itself from a very strong local supplier to an international reality. It took over 10 years but we got there, and for this I would like to pay tribute to the staff of Bobst Italia for their constant commitment to quality, which ensures that all the machines and services developed by the company have all the characteristics of excellence of BOBST products”, concluded Jean-Pascal Bobst, recalling all the loved ones who recently passed away in Italy due to the epidemic.
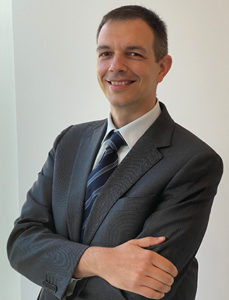
Face to face with Davide Garavaglia, CEO of Bobst Italia
How was this incredible 2020 and what prospects do you have for the next few years?
“2020 was certainly a very challenging year both from a human and an economic point of view. However, we were able to organize production in compliance with safety regulations to build the machines we already had orders for, especially thanks to the commitment and willingness of our employees who worked with passion despite the difficulties. For the future, we currently have orders that will allow us to face the next few months with relative confidence. Thanks to the global presence of BOBST group we have colleagues everywhere and we continue to maintain constant contact with the customer. Once this incredible period has passed, we see good prospects in particular with regard to the demand for sustainable and environmentally friendly materials and packaging with several ongoing projects on which we work with industrial partners”.
Multinational group with a global vision, with offices strongly rooted in the territory, is this perhaps one of the secrets of Bobst’s success in the world?
“Yes, certainly this is one of the strengths that gives two major advantages: the first is that our employees, sharing the culture of the territory, also develop greater loyalty to the company and strong motivation; secondly, the sharing of skills with colleagues around the world. Especially in this period of travel restrictions, it is thanks to the support of colleagues from local offices that we are able to install machines anywhere in the world”.
Can you tell us about an innovative packaging solution you developed that stood out during Covid-19 emergency and was appreciated by consumers?
“During the emergency rather than on future innovative solutions, we have prioritized the needs of our customers at the moment by making our Competence Center and our technicians available to print real production batches, thus helping them to meet the demands of brand owners”.
Packaging and sustainability: what is your vision and what concrete actions are you developing to satisfy the market?
“The individual projects are numerous but they share the fact that they are collaborations with suppliers of adhesives, inks, substrates and equipment with which we research and test solutions that meet the sustainability needs of packaging for different applications, especially in the food sector. These are collaborations that also include the main brand owners who are obviously parties involved also with the aim of marketing their products”.
How important are the new Competence Center, the R&D laboratory and the pilot line available to customers, brand owners and material producers?
“For a company that is part of a group that has a vision aimed at transforming the industry through innovation and sustainability, it is absolutely essential to be able to do research and test the feasibility of the solutions developed on machines. Solutions that cannot come separately from the different players in the production chain but that must be developed collaboratively starting from the conception of the packaging to its availability in points of sale and recyclability”.