With a double digital event, one in Italian and one in English, bfm presented on July 8th the new flexo stack printing machine Sirio S – Plus. Simona Colombo, sales and marketing manager and Marco Adamo, sales manager, did the honors by illustrating all technological innovations of the machine
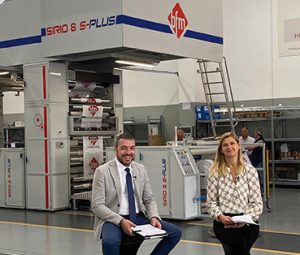
In the new recently inaugurated production area of 1500 sm, which are added to the 3300 of bfm headquarters, was born the Sirio S-Plus flexo stack printing machine, with 6/8 colors to guarantee excellent results and high quality printing on different materials, from plastic films to paper, for various fields of application, flexible packaging for food, pharmaceuticals, clothing and the classic shopper.
The new Sirio S-Plus, the result of internal research & development, offers not only high print quality but also efficiency and productivity thanks to easy and precise job changes, great flexibility of use, compact layout and modern design.
“The new Sirio S-Plus prints with water-based inks, in addition to solvent-based ones, on flexible plastic materials such as high and low density polyethylene, polypropylene, PET and also polymeric materials of different types even coming from raw materials of organic origin, in line with the environmental sustainability policies, that are very important for our company”, says sales manager Marco Adamo, who then goes on to describe the machine in detail, “from a design point of view the appearance is very similar to central drum machines, with linear polycarbonate carters and aluminum profiles. The printing units are completely protected by the carters and on the operator side there are transparent polycarbonate panels to facilitate greater control of the machine during printing phases. Front access from both sides is delimited by sliding protection doors equipped with all accident prevention safety systems. An important feature is the positioning of the electrical part on the upper deck of the machine, to reduce the footprint of the machine itself. The control console is equipped with an interface with a 22” monitor. The machine presented in the open house was equipped with three monitors due to the presence of the double front-back control camera. Another aesthetic feature, which however has important implications also from a structural point of view, is the printing unit that no longer comes with the classic printing decks, but with a compact shoulder that groups all the individual printing units “.
The new Sirio S-Plus in detail
From a functional point of view, the machine comes with a standard unwinder and has been designed with double station, with 3” or 6” spindles, capable of accommodating reels up to a maximum diameter of 800 mm. As an option, it is possible to request the revolver application or the hydraulic loader of reels with a diameter of up to 1500 mm. The machine is equipped with a double head oscillating web guide system for a perfect centering before entering the printing units, where each counter-printing cylinder is controlled by independent servomotors. The printing units are complete with plate and anilox sleeves, both of which can be replaced directly in the machine thanks to the cantilever system. The Sirio S-Plus is equipped with Easygear and automatic print presetting, thanks to these features job change can be carried on in total safety.
A “gear presence sensor” in installed on each plate holder to avoid collisions during the approach of cylinders. The printing groups positioning takes place completely automatically thanks to the positioning motors supplied by Bosch Rexroth, which allow you to switch from pause to work mode very quickly and precisely. The main advantage of this application is undoubtedly the possibility of storing production jobs. Doctor blades are closed chamber type, equipped with a basin for the ink recovery, while the quick change of the blades and side seals optimizes cleaning and maintenance phases. Sirio S-Plus also mounts 2 servo-motorized nip rollers , one at the entrance for 8+0 color productions, and one positioned in the center of the machine and useful for 4 + 4-color jobs. The drying system is equipped with 3 centrifugal electric fans, 2 of which for the delivery of hot air and one for the extraction of fumes. A drying box is positioned in the center of the printing unit when using the machine in 4 + 4 configuration. The temperature is controlled by an automatic thermoregulation system, with the advantage of reducing consumption. Also in this section are installed 2 cameras for front/back control of print quality. Then there is the winding section, 2 station revolver type, with automatic reel change and cutting, able to support reels up to 800 mm in maximum diameter. Also in this case, as for the unwinder, it is possible to foresee 3” or 6” air expanding shafts
Automatic inking and washing thanks to BFT Flexo system
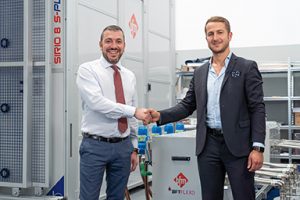
BFT Flexo, bfm’s partner for this event, provided the inking and washing system that operates on the new Sirio S-Plus. Simone Bonaria, owner of BFT Flexo, talked about it. “Traditional systems are essentially manual and therefore without automation, forcing the operators to continuously adjust speed and pressure of the pumps during production. Our inking and washing systems are completely automatic, and to start the work cycle it is sufficient to press a button on the touchscreen on the machine, or if integrated, it is possible to control the functionality directly from the main controls of the machine; the operator can set the speed of the pumps to optimize both inking and washing phases. The setting is recorded and linked to a specific job, so it can be recalled in the event of a reprint, with big benefits for process standardization. Moreover, thanks to the possibility of inverting the delivery pump, the system can recover all the ink, completely emptying delivery and return pipes and the doctor blade chamber, increasing ink savings and simplifying following washing phases. The innovative washing cycle ensures a deep cleaning of all system components thanks to 2 pre-washing and washing phases, guaranteeing a 50% saving of water or solvent. Finally, before changing the bucket, the system carries out an internal cleaning of the pipes on bucket side, thus avoiding any type of contamination of next color. In case of system inactivity for an extended time, thanks to a special algorithm, the system will carry out an internal washing cycle to ensure total cleaning. All the components of the system carry out a self-diagnosis showing the operator the current status and reporting in a preventive manner any necessary maintenance, avoiding in this way machine downtime”, Simone Bonaria concludes, underlining how much attention is today essential for the design and development of the so-called auxiliary components of a printing machine that contribute in a decisive way to the achievement of high results in terms of quality but also from an economic point of view.
Also the following technological partners participated in the event: Gama for the supply of viscometers, Tresu for doctor blade chambers, Apex for ceramic anilox rolls, Rossini for sleeves, Nu-Maber for the supply of the clichés and Sun-Chemical that offered inks for print tests.
“After the great success of the digital event, we will be happy to welcome customers at our headquarters in Solbiate Olona (VA) to give further technical details of the machine and we are sure that we will soon be able to meet again at trade fairs around the world, because nothing can ever replace the warmth and importance of human relationships”, concludes Simona Colombo.