On October 17, 2024, OMET hosted an open house at its Innovation Park and OMET Headquarters, where industry professionals gathered to discover the latest solutions for packaging printing: the event demonstrated OMET’s continued leadership in the packaging printing industry, offering innovative, sustainable, and highly flexible solutions designed to meet the increasingly diverse needs of modern printing companies
The event began with an introduction by Marco Calcagni, OMET’s Sales & Marketing Director, who remembered, after a short history of Omet, that the company serves big groups, among them there are CCL, CTI Group, Constantia Flexible, Labelmarkers, Multi-Color, Eurostampa, All4Labels, Huhtamaki e Master press, but for Omet “all customers are equally important, because they are a resource for us, our goal is to make our customers earn and develop, because if they do well we can also innovate and invest”.
Roberto Speri, Area Manager and Product Manager, then explained how OMET’s technological advances are driving the transformation in the printing sector, to be more sustainable. He analyzed in detail the possibilities offered by the Omet Varyflex V4 (EB wet/Wet-UV Wet/Wet- UV Wet/Dry): the machine is based on an offset platform with sleeve technology, and reaches a maximum mechanical speed of 400 meters per minute. The machine can print multi-layer substrates because a patented system allows the use of triplex and even quadruplex material with an aluminum layer cured by EB, all at high speeds without the need for post-print lamination. Braille characters and tactile pictograms printing is obviously also possible thanks to two bars to match multiple job configurations with automatic mark alignment. The machine is completely modular and can be configured according to the needs of the job to be printed.
In the offset unit we find another patent relating to the fixed plate shaft, the blanket shaft with circular movement and the impression roll with linear movement. The ink duct has independent sectors that guarantee high precision of the inking and stability; the ink train has 19 rollers and temperature control, the form rollers are four and three are equipped with a special anti-ghosting oscillation system; the dampening is constant but differentiated.
And the conversion from offset printing unit to flexo and/or gravure: fast and easy! Vertical flexo printing is also possible, which can be set with various configurations. The gravure unit has a new design and guarantees excellent accessibility from both sides, and allows front and reverse printing.
One of the key strengths of the Varyflex V4 is its fast job changeover, which, thanks to the Easy Sleeve Format Change system, allows for a complete format change in a very short time in a simple, fast, and, most importantly, safe manner. This significantly reduces job changeover times and increases operational flexibility, making it ideal for both short and long runs.
Thanks to OMET’s advanced tension control systems, the Varyflex V4 maintains optimal print quality on various substrates, minimizing waste and ensuring consistent results. The automatic pre-register and Vision system further reduced setup times, bringing each job to perfect register with minimal effort and material waste.
Speri then underlined that the Omet Varyflex V4 guarantees sustainable printing because it has low energy consumption, EB drying does not produce VOCs, consumes less ink, produces less waste and does not use solvents.
EB technology, EB inks: all for a more sustainable print
Brian Sullivan, Vice President of Marketing and Sales at Energy Science Inc., emphasizied how Electron Beam (EB) technology is becoming the leading solution for eco-sustainable printing. ESI is a leader in EB treatment with many installations of EB systems on web offset machines all over the world.
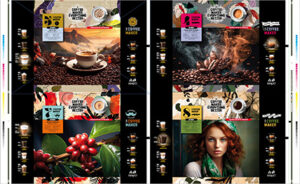
EB technology involves a system that accelerates electrons and projects them into the substrate (the electrons are generated by passing an electric current through a tungsten filament and then accelerated in an applied electric field), this beam causes molecular changes, and the dose and energy density are modulated depending on the application. The advantages are many: first of all, energy consumption is low, the treatment is suitable for food packaging, there are no odors, no photoinitiators are needed, resistance to heat, scratches, abrasion and chemicals is high and the result is a brilliant substrate.
Norbert Wünsch, Zeller-Gmelin, once again highlighted the advantages of EB inks and highlighted that the use of this technology is increasing. The company offers the Esalux E4 range for offset printing. Thomas Ellinger, Actega, closed the series of interventions with a discussion on the latest regulatory updates for UV Varnishes.
Demonstrations on the Varyflex V4
After the presentations, attendees witnessed a live demonstration of the Varyflex V4, a printing machine with combined offset/flexo technology dedicated to flexible packaging printing. The machine was presented with an 850 mm web width but is also available in widths of 670 mm and 1080 mm. It showcased its versatility by handling a wide range of materials, such as unsupported films, multi laminates, and folding carton.
During the demonstration, the Varyflex V4 printed a coffee packaging on a 12-micron PET film using a combination of 4 EB offset colors and an EB flexo white. The hybrid printing process, executed at 300 meters per minute with a Wet-on-Wet configuration, demonstrated the machine’s ability to combine offset quality with the coverage of flexo white, all dried with Electron Beam technology. The quick job changeover, completed in just 10 minutes, showcased the machine’s efficiency as it effortlessly switched to a 350-gram cardboard substrate, producing high-quality photographic prints with glossy and soft-touch finishes.
During the demonstration, Roberto Maiocchi, Sales & Marketing Manager of BST eltromat Italia, a long-standing partner of OMET, provided valuable insights into the print quality control system, explaining how BST control devices integrated into OMET machines enable real-time quality monitoring, ensuring excellent and consistent results even during complex jobs.
The day ended with a tour of the OMET production department where it was possible to discover the advanced production processes and technologies that are the basis of the company’s success.