Battistella Capsule has been serving the wine industry since 1961, and the goal has always been to provide the customer with a high quality product to dress the bottles. An artisanal work, which also thanks to partnerships with excellent suppliers such as R.C.L., guarantees high quality and industrial-type production, always in the wake of tradition. We talk about it in this article with Mario Battistella and in the in-depth video with Giovanni Basile Operations Manager of Battistella Capsule and Bruno Giorcelli of R.C.L.
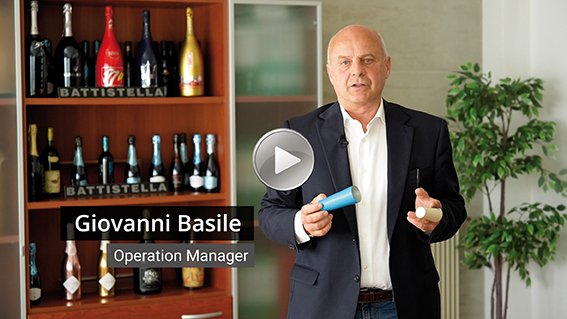
It is one of the most loved and repeated gestures when it comes to starting a moment of celebration, a toast, or even just a good dinner in company. Once you grab the tab, and the game is done, in a few seconds, removed the aluminum wrap and the wire hood, the bottle cap is opened and you can begin the convivial moment where the wine always plays a starring role. In this gesture of opening the bottle, which all of us have all done many times, there is a world of passion and craftsmanship, attention to detail, listening to the customer’s needs and the search for the highest quality, to dress in the best way a noble product of food and wine excellence.
To tell the success story involving two Italian companies, we went to Ceggia in the province of Venice, where Battistella Capsule is based, a historic company in the wine capsule production sector, which in 2017 established a partnership with R.C.L. the manufacturer of narrow web gravure printing machines: the company has already installed 3 printing machines, a Rotoshaftless 350 and 2 Rototestine, the last of which, the 220 model arrived at the beginning of this year.
Battistella Capsule has been serving the wine industry since the 1960s
The company was founded in 1961 from the idea of brothers Angelino and Filiberto Battistella, passionate mechanical builders who, also thanks to the geographical location, we are in fact in Veneto, on the slopes of Prosecco hills, where wine is more than just a product, decided to dedicate themselves to the capsule sector for the wine sector, also following the natural evolution of a market which over the years has led the product to be considered a true excellence. And like any excellent product, wine also requires an ad hoc dress, with the label playing an important role, as do the aluminum capsules that cover the neck of the bottle.
“The wine market was growing, also from a technological point of view with regards to bottling, but we were not witnessing technological development to the same extent for the machines that produced capsules”, says Mario Battistella, today at the helm of the company family, “consequently we have always designed and built the machines for this particular production internally, at least at the beginning”. In fact, it is thanks to a Battistella patent, later sold to another company, that today there are technologies capable of applying capsules on bottles.
Today the situation has changed, and although in the capsule production department there are still machines built internally, there are also new technologies from leading companies.
“Throughout our history, we have grown, always in step with the needs of a market which today is certainly industrial, but where craftsmanship and attention to detail, partnership and dialogue with customers and suppliers, represents an essential element of our way of working”, adds Mario Battistella.
Today the company has achieved a market position of absolute importance, it exports internationally, has a cutting-edge fleet of machines with around 100 collaborators and commercial partners all over the world.
A simply complex manufacturing process
Mario Battistella, speaking about the production process of wine capsules, likes to define it as simple and complex at the same time. Simple because there is the use of two main materials such as aluminum, also coupled, and heat-shrinkable plastic materials, whose reels are printed in gravure and then cut into smaller reels, which, in the company’s second factory a few hundreds of meters from the headquarters, are transformed into finished capsules ready to be delivered to the customer for bottling.
“The qualitative aspect and precision are essential in our production, since stopping a bottling plant that runs at 15 thousand bottles an hour would be detrimental. The production process is apparently simple, since we are talking about gravure printing and creation of the capsule. However, in the middle all there are customizations, particular graphics, tolerances and …. the embossing that all together give life to the final aesthetics of the product, with the guarantee of machinability, which doesn’t allow errors. Today, thanks to technology on the one hand and know-how on the other, we are able to satisfy any type of request from our customers, who operate in a highly competitive market such as the wine one, and so they must increasingly differentiate themselves”, intervenes Eng. Giovanni Basile Operations Manager of Battistella Capsule, who in this regard will soon launch a new department for the production of metal wire-hoods for closing the cap, with a view to diversification but always within the range of products for the wine supply chain.
The strategic partnership with R.C.L
Always looking for a technological partner capable of satisfying the needs of this market, characterized by short runs, frequent changes and extremely small web dimensions (22 cm), Mario Battistella, having not found anything that was right for him, was forced to build his own gravure machines to print his capsules, with all the problems involved. “With the evolution of the market, the requests for multi-color printing and increasingly shorter runs, we started looking for a manufacturer who would listen to our needs and with whom we could develop together a machine that would fully respond to our requests”, adds Mario Battistella.
The completely casual meeting with Bruno Giorcelli, one of the owners of R.C.L., allowed to finally write a new chapter in the history of Battistella Capsule, and since 2017, the year of the first installation, now there are already 3 R.C.L. machines. who work at an incessant pace in the Ceggia production site, the latest of which is the recently installed Rototestine 200.
“Bruno Giorcelli listened to me and thanks to the dialogue we established, we finally managed to have the machines I had always wanted. R.C.L. accepted the challenge, questioning himself and also reviewing some details in the machines we purchased, so much so that we are already thinking about purchasing a fourth machine”, says Mario Battistella.
This partnership has therefore opened a new era in the narrow web gravure printing press sector; RCL has hit the mark and the offer of highly customized machines has gradually acquired space in the market towards accurate production, which tends to cancel out all the efficiency losses typical of large systems if intended for the production of small runs.
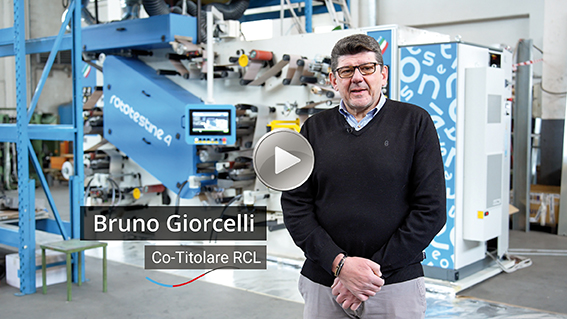
The new Rototestine 220 in detail
The new Rototestine 220 represents a concentration of technology in a monobloc line, extremely compact and suitable for the production of small batches thanks to the cantilever technology of the printing cylinders, whose particular position has allowed to reduce the dimensions of the machine and consequently of the web path. The particular 3-layer drying hood allows the machine to print at a speed of 150 m/min. Thanks to the collaboration with Battistella, customizations were introduced such as the vault bar and an additional tunnel, which made it possible to complete the work potential of the machine, which in the configuration envisaged for Battistella allows the printing of 4 colors, with 1 color in register with back printing, in-line cutting up to produce 30 mm discs with winding in two axes at a speed of 150 m/min, with a single operator and with waste reduced to a minimum.
“Also from our point of view, the partnership with Battistella was a pleasant challenge, and by combining our technical and manufacturing skills with theirs as printers of an extremely particular product such as wine capsules, we have developed machines in line with customer expectations. We certainly took a challenge, also reviewing some of our ideas and this was made possible thanks to a real relationship of mutual exchange with Mario Battistella and all his staff”, concludes Bruno Giorcelli.