DuPont as a leading company is called upon to provide the market concrete answers on sustainability. This serious commitment that can no longer be postponed was the focus of discussion at last september company meeting where the latest trends and technological solutions to translate theoretical dictates into concrete actions were analyzed with industry experts
Sustainability is now a must for any type of manufacturing business, and flexo packaging printing is not exempt. But, if until a few years ago it was talked about as an almost abstract subject, with very futuristic time horizons, this is no longer the case, and leading companies such as DuPont are questioning themselves internally in order to be able to provide concrete answers and solutions to their target markets. It is the customer who is asking for it, and the industry can no longer be caught unprepared.
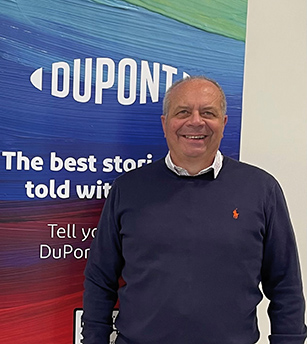
“When we started talking about sustainability in 2008, the word sustainable was little more than a slogan. Today, for us being sustainable means developing specific products so that we can obtain a packaging that is more sustainable, with a final cost aligned with the traditional one and printed with the same quality standards”, says Mario Castelli.
DuPont has always been committed to the sustainable development of the industry, and there are many questions that need to be answered. Climate change is undoubtedly at the top of the list; it is now quite evident how much human activity affects the climate, and what seemed unthinkable just a few years ago are now tangible issues that are there for all to see. The environmental one is certainly an important aspect, where we always start to address sustainability, but it is not the only one. Today it is increasingly clear that sustainability is a path that each reality, with the help of specialized consultants, can build itself to give the market those answers and reassurances required to create trust in a brand.
But above all, environmental sustainability, as also emerged during the last Gipea conference, must also go hand in hand with social and especially economic sustainability. Because it is true that everything has a price, and sustainability costs money, but then is the market that always has the last word.
Sustainability in the packaging industry: a common goal
Sustainable growth, which today all technology but also service providers should aim at, is not just a phased program to improve the environmental performance of their proposals, but a comprehensive way of working to deliver significant economic value and open new opportunities. Operators for their part should abandon the idea that sustainable technologies are just a compromise or marketing operations, because today the sustainable revolution is here and it is disrupting all sectors. It is good for the environment and society, but it puts pressure on everyone, suppliers and users.
Everywhere we keep hearing this word, even at the recent K trade show, the world’s most important exhibition for the plastics industry, the leitmotif was this, and indeed we noticed a great excitement translated into concrete solutions, by companies operating in the world of plastics, traditionally under the eye of the storm and consumers who are often led to consider this material as unsustainable when in fact today the main aspect is to evaluate its functionality in relation to the task called upon to perform and its effective recyclability, without forgetting that almost always the environmental impact of the product contained in the package is greater than the package itself, which must protect, transport and thus ensure that a food is not wasted. And we know how food waste is another aspect to consider in the sustainability journey.
Webinars, events and association meetings have sustainability as a major theme. One thing that certainly emerges from all this discussion and comparisons is the importance of the need to measure sustainability, and the best tool to do so and to counteract greenwashing is the LCA, an objective process of assessing the environmental impact associated with a product, service or activity, throughout the entire life cycle of a product, to understand what are the main contributions to the environmental impact of a product or of a service and then act to eliminate them. This analysis is especially important because it is clear that there are no universal recipes or pathways to becoming sustainable; everyone, from the individual to the company, must build them for themselves. Equally clear is that no person or company will be 100% sustainable, but the important thing is to get as close to the goal as possible.
Cardboard or plastic?
What about the impact of packaging? Those made of cardboard are defined as environmentally friendly by their very nature; they are 100% recyclable and biodegradable, and recycled cardboard does not last less or is less durable. Instead, the main characteristic of flexible packaging is its light weight; the weight of the packaging, and therefore of the finished product, during transport and storage is less, and the weight and volume during disposal, when it becomes waste, are less. Very important is the design aspect of packaging, so the design phase should be considered as the starting point so that a package can be designed for reuse and at the end of its life, for 100% recycling.
It could be argued that although cardboard requires less energy to be produced it uses more water and produces a large amount of solid waste, plus cardboard is heavier and bulkier so it produces more CO2 emissions associated with transportation. But cardboard is derived from a renewable resource and is increasingly produced using renewable energy and is more easily recycled. Further to plastic, recycling rates are increasing, although cardboard recycling rates are three times as high and cardboard products are made from recycled cardboard.
In short, many pros and cons, but ultimately the primary goal, regardless of whether you choose to use plastic or cardboard packaging, is to reduce waste, thus reducing the materials used to produce it (plates, chemicals, inks), reusing packaging and recycling as much as possible. And in this journey everyone is called upon to play a role, sharing experiences and information among all the stakeholders in the supply chain, from the producers of materials and technologies, down to printer-converters and finally the large-scale retail trade and consumers.
DuPont carried out internally a Life Cycle Analysis focused on the differences and impact between flexo and gravure printing using the example of flexible packaging, and then, in the flexo area platemaking comparing solvent technology and thermal development, with an in-depth analysis in the world of flexo printing on corrugated board and for paper bags.
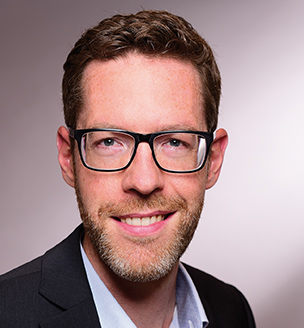
What about plates? Obviously, the optimal plate is the one that can provide the highest print quality, on sustainable and cost-effective substrates.
We discuss this in this interview with Christian Apenberg, Regional Marketing Manager EMEA & AP – Cyrel® Solutions at DuPont and Mario Castelli, Sales Manager Southern Europe and Northern Africa – Cyrel® Solutions at DuPont.
Thinking ahead to 2030, which concrete actions will DuPont put in place to achieve sustainability goals?
“DuPont has committed to setting science-based targets to reduce greenhouse gas (GHG) emissions in line with the Science Based Targets initiative (SBTi), a partnership between CDP (former Carbon Disclosure Project), the UN Global Compact, World Resources Institute (WRI) and the WWF.
This includes concrete reductions of Scope 1 and 2 emissions by 2030 – goals, which the Cyrel® Solutions business will most likely over-achieve. DuPont also committed to deliver zero carbon emissions by 2050.
At DuPont™ Cyrel®, we are continuously working on reducing the environmental impact of our products as well as providing our customers with an optimized workflow for both solvent and thermal solutions. There are several projects being worked on and the results will continuously be reported in updated LCAs. It is especially important for us to look at the full picture, which includes the raw materials we use to produce our products, packaging to provide the most efficient systems, workflows and consumables to ensure also our customers can improve their environmental footprint. Recent examples are in the updated LCA, which states an overall benefit of 38% lower CO2 for the thermal Cyrel® FAST workflow process compared to solvent – but also developing a new solvent, Cyrel® Flexosol-X, that eliminates hazardous components as well as providing up to 50% lower VOC emissions”.
Materials, technologies, and sustainability – DuPont solutions for the needs of the markets: flexible packaging, labels, corrugated board
“We understand that different customers have different needs, we are able to support customers on their sustainability journey and we have to start taking actions today. We truly believe in Flexography as the lowest impact technology for flexible packaging printing, as proven by our LCA. It generally consumes less solvent and energy and produces less startup waste.
Platemaking for these applications can be optimized by going thermal: Cyrel® FAST consumes less electricity compared to a solvent workflow (up to 81% less, according to a recent study based on internal and external data) and avoids the use and handling of organic solvent completely.
For corrugated applications, where plates with deep relief requirements are dominant, we support our customers in different ways: by providing thinner plates, supported by mounting foam, contribute to reduce environmental impact. In addition, maybe even more important is supporting the industry trend of using cardboard with higher recycling content that is often more difficult to print on. DuPont™ Cyrel® has developed photopolymer plates like Cyrel® DLC for corrugated postprint and Cyrel® ESM for paper/corrugated preprint that deliver higher print quality even on demanding substrates. With that, we allow converters and brand owners to go for materials with lower environmental impact – without taking a hit on print quality”.
Will the future increasingly favor thermal technologies, or will there still be room for solvent-based ones?
“DuPont has been a pioneer on the thermal flexo platemaking and the industry confirms its suitability for many applications – not only for sustainability reasons. Since the introduction of Cyrel® FAST over 20 years ago, far more than 1,500 units have been installed and we continue to innovate with our latest generation systems Cyrel® FAST 2000 TD and 3000 TD. We do expect a further growth of the thermal process.
Nevertheless, we do not abandon solvent systems. Our recent product launches (non-hazardous and low-emission Cyrel® Flexosol-X solvent, Cyrel® EASY R plate series in thermal and solvent and the LED-exposure optimized Cyrel® Lightning LSH) confirm our commitment to support both workflows”.
In your experience, how important are the sustainability credentials toward the end customer of a player like DuPont to the purchasing decision for products and technologies?
“We have experienced high interest in data-supported sustainability declarations. Many of our direct and indirect customers are working to achieve sustainability goals and we, as a material and system supplier, can support assessing the status-quo by providing fact-based information. In the current economic environment, sustainability may be deprioritized again for shorter term goals, but achieving sustainability requirements will increasingly also be a competitive and financial requirement”.