The focus of the fifth of the Nordmeccanica Events, a series of live shows from the company’s headquarters in Piacenza and broadcast all over the world via satellite, was sustainability: we spoke with Giancarlo Caimmi, Nordmeccanica’s sales director, to understand how synergies in technology of lamination, barrier coating and vacuum metallization can support the evolution of flexible packaging sector
Nordmeccanica’s commitment to sustainability is articulated on several fronts to meet the needs of the circular economy advanced by manufacturers of packaging and processors. The company, as a member of the value chain of one of the most critical sectors, namely the food sector, actively participates in all the developments required by the sector and produces an important number of proposals and innovations related to its specific segment. Participating in industry developments means responding to requests and needs expressed by other members of the value chain. From time to time you have to adapt the design of the products as well as the development of new technologies.
Face to face with Giancarlo Caimmi, Nordmeccanica’s sales director
Let’s start with the technical description of the laying down process of the ALoX layer?
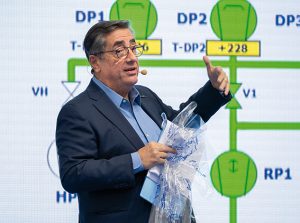
“AlOx is a metallization technology that allows a thin layer of oxidized aluminum to be deposited on substrates for flexible packaging. It is made with machines called metallizers where aluminum evaporates in a vacuum chamber and is deposited on a plastic film by condensation. The oxidation obtained by means of a controlled oxygen injection in the flow of aluminum vapors causes a reaction between aluminum and oxygen, generating aluminum oxide (AlOx). The compound is transparent if the process is properly controlled. Consequently, it makes it possible to increase the barrier to agents that potentially degrade the contents of the packaging (essentially water vapor gas), while, thanks to transparency, it allows the consumer to view the packaged product. The increase in the barrier effect makes it possible to extend the expiry date of the product and at the same time to simplify the composition of the packaging by reducing the number of layers. In practice, it is possible to eliminate film layers that contribute to barrier towards gas. The final goal is the composition of a mono-material packaging that represents the ideal solution for the needs of packaging recycling”.
What are the characteristics of the machine that allow the process to be carried out in detail?
“These are machines in which the production process takes place inside a vacuum chamber. The vacuum allows to lower the evaporation temperature of the aluminum and make the process efficient from an energy point of view. Inside the vacuum chamber, thin aluminum wires are directed to evaporators placed in correspondence with the material to be “metallized”. The aluminum in the vapor phase comes into contact with the film which at that point is supported by a cooled cylinder. The final effect is the condensation of aluminum on the surface of the material. The material, generally a plastic film, but can also be paper, is placed inside the vacuum chamber in the form of a web on an unwinder. A certain number of support rollers allows the material to be sent to the metallization area and then to the winder in which the film, at this point metallized, returns in web form”.
What are the technological trends involving metallization machines?
“Metallizers have been an industrial reality for decades. They have developed in technology and efficiency with the increase in needs related above all to food packaging. Over the years there have been significant developments related to increasing both production and energy efficiency. Developments mainly related to the design of these machines. At the same time, there have been developments linked to the need to develop new technologies based on metallization. As a result, technologies such as “pattern” metallization have been developed, that is the possibility of depositing aluminum not on the entire surface to be treated but in specific areas, for example by creating transparent windows. More recently, the refinement of this technology has made it possible to deposit the aluminum as if it were an ink, obtaining printing effects with the benefit that the metal applied in the form of logos or other designs makes possible security and anti-counterfeiting applications. The AlOx we were talking about at the beginning of the interview is another significant example. One trend to take into consideration is also that of the size of the machines. The need to make the process more efficient had generated in the last three decades the tendency to “enlarge” the machines. In other words, the wider the web width, the more efficient the process will be. This had led metallizers manufacturers to build them with a web width well over three meters. The price to pay was the loss of flexibility and the ability to adapt to market demands efficient and low-cost production. This has generated a reversal of the trend that now sees machines with 1.5 meters web width conquering interesting market shares”.
What does Nordmeccanica’s vacuum portfolio include?
“Nordmeccanica’s portfolio in the Vacuum division covers all the dimensional and technology ranges discussed above. We can offer specific products that cover the needs of the narrow web and products that cover the needs of the wide web: in total the range covers the dimensions from 1.3 to 3.4 meters of web; we have in our catalog all the most modern technologies developed as part of the metallization process, offering options that allow you to configure our models for the production of pattern metallization, AlOx, high barrier. In fact, our offer covers the widest range of solutions available in the specific sector”.
Some details about La Molisana case story (laser cutting)?
“La Molisana, one of the high-end brands among Italian pasta producers, was the first to base its packaging philosophy on a massive use of paper. It would seem like a great return, in fact pasta was packaged in the paper at the dawn of packaging history. This is not the case, modern hygiene requirements in packaging require the presence of a plastic film in contact with the product for better shielding. The use of a uniform layer of paper would then have prevented the consumer from seeing the product. The solution was the development of laminators in which the lamination between the paper and the plastic film of the final packaging occurs after creating in the paper layer the window that allows you to view the product. This window is made by means of laser cutting in a flow that involves glue spreading on the paper, removing the window with laser cutting, laminating to the film. Nordmeccanica has integrated the laser cutting unit inside the laminator in partnership with the Italian leader in the sector SEI Laser”.
Finally, let’s talk about the differences and specificities between Asian and European markets?
“In our sector, the various geographical areas are characterized by market trends influenced by both economic and cultural factors. Asia is a constantly growing and evolving market, Europe and America are more mature markets where trends have stabilized enough. Most of the world production of metallized materials is concentrated in Asia. The largest number of plants are sold in that area and they are almost all large plants. In Europe and America the choice to move towards flexibility and to align with the trends in the circular economy is developing more rapidly. However, we are still in a phase of defining the trends that will stabilize and consolidate in the coming years when the culture of safeguarding resources will prevail in an increasing number of countries”.