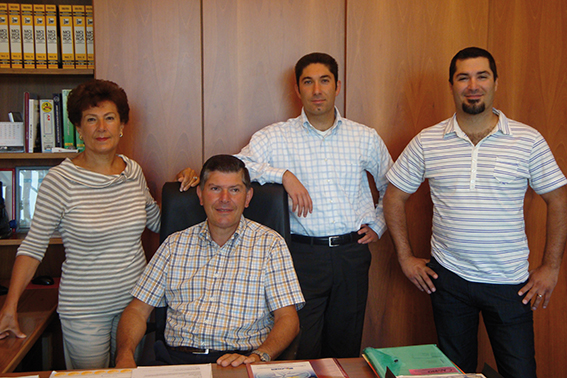
L’azienda di brenna (Co) specializzata nella stampa e trasformazione di imballaggi flessibili, in particolare per quelli microforati per il confezionamento di prodotti alimentari, è stata protagonista del lancio di un prodotto, il caffè in capsule, capace di stravolgere le abitudini di consumo in ogni parte del mondo. Una rivoluzione partita proprio dalla provincia di Como…
Quella di Corapack è una storia incredibile per certi versi, e testimonia ancora una volta se ce ne fosse bisogno, che spesso le opportunità sono alla portata di tutti, ma a fare la differenza è il fiuto dell’imprenditore, capace di guardare oltre. Ma andiamo con ordine, l’azienda viene fondata a Cantù nel 1982 da Massimo Radice, molto attivo anche a livello associativo, in Atif, dove ha ricoperto la carica di Presidente. La formazione tecnica del Sig. Radice, 12 anni in una multinazionale del settore plastico, lo ha portato a dedicarsi alla ricerca e sviluppo di nuovi prodotti nonché all’acquisto delle materie prime, mentre a sua moglie Mariateresa Colombo, che ha fondato insieme a lui l’azienda, grazie alle competenze in materia finanziaria, ha lasciato la gestione amministrativa. “Se penso che la nostra avventura è iniziata nel 1982, in un piccolo capannone con 2 operai, e oggi ci ritroviamo su una superficie di 12.000 metri quadri, occupiamo circa 50 persone, e siamo un punto di riferimento internazionale nel settore del film microforato per imballaggio, non posso nascondere una certa soddisfazione”, esordisce Massimo Radice, che oggi è affiancato nella gestione aziendale dai figli Fabrizio, oggi direttore generale e Michele, responsabile di produzione.
Dal film microforato per pane a quelli per i filtri delle capsule di caffè: un successo globale
Corapack fin da subito si specializza nella produzione di film microforati per l’industria della panificazione contribuendo a sviluppare il lancio di questi prodotti nei supermercati. Il problema era offrire un prodotto che fosse in grado di confezionare il pane ancora caldo, evitando che il calore creasse condensa e umidità, compromettendo sapore e consistenza del pane. Dal pane ai prodotti ortofrutticoli, i film microforati hanno rappresentato una straordinaria opportunità per la commercializzazione di questi alimenti all’interno delle catene di supermercati che in quegli anni iniziavano un percorso di grande espansione, offrendo ai consumatori la possibilità di gustare prodotti freschi con una durata a scaffale più lunga e una sicurezza maggiore garantita dall’imballaggio.
Corapack inizia quindi la propria attività con un primo micro-foratore ad aghi caldi, quando ancora la stampa flexo non era per nulla considerata all’altezza della rotocalco, pertanto anche nel packaging veniva utilizzata per lo più per stampare testi a uno massimo due colori, per indicare la scadenza del prodotto o un codice a barre. Nel corso degli anni, i micro-foratori crescono e oggi Corapack ha un reparto dedicato con 6 macchine per la perforazione a caldo, due macchine per la macro-perforazione, una per la perforazione laser, taglierine-ribobinatrici, macchine speciali sempre per la produzione di film microforati da imballaggio. Seguendo un percorso evolutivo a ritroso, Corapack ha inserito anche 2 macchine da stampa flessografica, l’ultima delle quali installata a fine 2019; si tratta di una Koenig&Bauer Flexotecnica Evo XD di ultima generazione, che ha affiancato una Comiflex, anch’essa acquistata nuova solo 4 anni fa. Completa il reparto un’accoppiatrice Simplex di Nordmeccanica, macchina sulla quale vedono la luce gli speciali film accoppiati in duplice e triplice strato per i filtri delle capsule del caffè, un prodotto che ha reso celebre Corapack nel mondo, supportando multinazionali del settore food&beverage nel lancio mondiale delle ormai famosissime capsule per caffè.
Dal pane, ai film microforati per ortofrutta il passo è breve, e grazie a un progetto portato avanti insieme a Coop Italia nascono le vaschette confezionate con film microforato, capace di preservare prodotti delicati come le fragole allungandone la durata sul banco del supermercato, mantenendo intatti la forma e il gusto del frutto, che altrimenti veniva confezionato con film estensibile, causa di danneggiamenti irreversibili al prodotto. “Grazie a questo progetto con la Coop, fummo in grado di introdurre un nuovo concetto di confezionamento nel settore ortofrutticolo della grande distribuzione, sviluppando ulteriormente il processo di micro-perforazione e arrivando a scegliere per alcune tipologie di prodotto la macro-perforazione a freddo del film con asportazione totale del coriandolino di film in eccesso, per evitare problemi di micro-puntinatura sulla buccia dei prodotti, determinata invece dal processo di micro-perforazione a caldo, che per sua natura fonde il film, creando una sorta di anellino di materiale fuso attorno al foro, il quale a sua volta crea un’ombra che viene proiettata sul frutto, creando appunto una micro-puntinatura antiestetica.
Quando una telefonata cambia la vita…
Nella seconda metà degli anni 2000 si sono iniziate a sviluppare le capsule per il caffè, dando vita di fatto a una vera e propria rivoluzione, capace di stravolgere le abitudini dei consumatori, creando un nuovo settore. A raccontarci il contributo determinante di Corapack nello sviluppo di queste capsule è Fabrizio Radice, laurea in ingegneria chimica macromolecolare che abbinata a un’innata capacità relazionale e commerciale, lo hanno portato a seguire in prima persona il progetto che ha di fatto cambiato, in meglio, le sorti dell’azienda di famiglia. “Le prime capsule per caffè erano costituite da materiali plastici rigidi con tappi filtro, che ne rendevano difficile lo smaltimento a fine vita. Nacque così l’esigenza di introdurre un film che potesse fungere da filtro, e iniziammo a condurre dei test con un leader italiano nella produzione del caffè, che però mise da parte il progetto”, esordisce Fabrizio, dando vita a un racconto incredibile – “ricevetti una telefonata anonima, che decisi di ascoltare nonostante il grande scetticismo iniziale. Dall’altra parte del telefono avevo una persona che non si qualificò, ma che una volta capito che potevamo fare al caso loro, mi diede appuntamento per la mattina seguente alle 9 nella loro sede svizzera. Partii prestissimo per essere puntale all’appuntamento, non ci fu nemmeno il tempo di firmare tutti i patti di riservatezza del caso, perché eravamo a ottobre e a gennaio la multinazionale sarebbe dovuta uscire sul mercato con queste nuove capsule con filtro in film microforato, ma che insieme ai loro abituali fornitori non erano riusciti a sviluppare. Fui chiuso in una stanza, lasciai il cellulare in una cassetta e mi fu chiesto di giurare che mai e poi mai quello che avrei visto e di cui avremmo discusso sarebbe in alcuna maniera uscito da quelle quattro mura”, racconta Fabrizio.
La sfida era enorme, perché bisognava trovare una soluzione da commercializzare in meno di due mesi. Corapack, che non aveva mai lavorato con multinazionali di questo tipo, ma forte del know-how e della voglia di cimentarsi in questo innovativo progetto, raccolse il guanto, e iniziarono settimane frenetiche fatte di numerosi test, viaggi in Svizzera, visite in azienda da parte di ingegneri e tecnici. “La difficoltà principale di creare questi film microforati per le capsule del caffè risiedeva nel fatto che le tolleranze erano praticamente a zero, quindi era necessario da parte nostra adottare una serie di procedure e misurazioni di controllo per rispettare gli standard rigidissimi imposti dal cliente. Dopo diverse modifiche, riuscimmo a sviluppare il film microforato in maniera tale che la funzione di filtraggio richiesta fosse perfetta per l’erogazione del caffè e nel gennaio 2007 il prodotto fu lanciato sul mercato come oggi lo conosciamo, con un volume di vendita di 1,5 miliardi di capsule annue. Con grande soddisfazione e un pizzico di orgoglio, possiamo dire che dietro quel successo planetario, ci siamo noi di Corapack, una piccola azienda capace di supportare una multinazionale leader assoluta nel lancio di un nuovo progetto”, aggiunge Fabrizio. Ovviamente questo progetto ha aperto le porte anche ad altre successive commesse da parte di questo gruppo, facendo diventare Corapack un punto di riferimento importante. Ancora oggi, caduti i brevetti internazionali, l’onda lunga di quello straordinario progetto è fortemente presente, e sono diverse le chiamate che Corapack riceve da ogni parte del mondo da parte di produttori di capsule che chiedono il loro supporto.
“La multinazionale, per volumi produttivi ma anche per policy che non le consente di avere un unico fornitore, ci ha chiesto di condividere con altri fornitori la nostra esperienza, così da poter avviare in altri stabilimenti gli impianti per la produzione di questo film, e anche questo è stato un motivo di orgoglio, una piccola azienda come la nostra fu quindi chiamata per insegnare ad aziende del nostro settore molto più grandi noi, anch’esse multinazionali. Da un punto di vista della produzione, per noi questa commessa ha significato mettere a disposizione per questa lavorazione una delle nostre 6 linee di micro-perforazione, perché è vero che la commessa è importante, ma parliamo alla fin fine di un supporto di pochi cm quadrati”, aggiunge Fabrizio, sottolineando che essere venuto a contatto con una multinazionale ha consentito a Corapack di compiere anche un salto di qualità nelle procedure, nel modo di produrre e di relazionarsi col mercato.
Nuovi progetti per materiali da imballaggio compostabili
L’altro grande filone che vede l’ufficio R&D di Corapack impegnato incessantemente nello studio e sviluppo di nuovi materiali è rivolto al mercato dei film compostabili. Ancora una volta a stimolarne la richiesta è il settore ortofrutticolo, che già dalla metà degli anni Novanta con l’avvento dei primi prodotti biologici ha di conseguenza iniziato ad avanzare richieste di film da imballaggio compostabili, per trasmettere anche nella confezione il principio di acquisto quasi filosofico, che si cela dietro l’acquisto di un prodotto bio.
L’esperienza acquisita da Corapack nel corso degli anni nella gestione di materiali compostabili ha consentito all’azienda di raccogliere anche l’ultima sfida, sempre riguardo le capsule di caffè, che oggi per forza di cose devono essere prodotte con plastiche compostabili, inclusi i film facente funzione di filtro. “È da circa dieci anni che commercializziamo film compostabili per le capsule del caffè, e adesso siamo pronti per l’ultimo passo, ovvero realizzare materiali che siano compostabili a livello domestico, e non solamente industriale, dove è richiesto un impianto di compostaggio. L’obiettivo è arrivare a immettere sul mercato una capsula del caffè che sia conferibile nella frazione organica”, conclude Fabrizio Radice, che dall’alto della sua formazione di chimico dei materiali, lancia l’ennesima sfida per il settore del packaging: ridurre il più possibile i materiali da utilizzare per poi ragionare in maniera seria, efficiente ed efficace in termini di riciclo, a partire dalla raccolta domestica con cestini dedicati, e salendo lungo tutta la filiera, fino agli impianti finali, utilizzando materiali compostabili per tutta quella serie di prodotti che sporcano e contaminano gli imballaggi, che quindi diventano poi difficili da riciclare.
Un’attenzione alla sostenibilità che per Corapack significa essere coinvolti in prima persona, a partire da un processo di produzione e un’organizzazione flessibile ed efficiente della struttura sapientemente gestita e coordinata da Michele Radice volta a ridurre al minimo gli impatti sull’ambiente, perchè è vero che la capacità di rispondere velocemente agli stimoli del mercato dipende dalla capacità di ascolto e sviluppo, ma alla base è indispensabile un’adeguata e solida struttura. L’azienda impiega energia elettrica proveniente dall’impianto fotovoltaico che copre il proprio stabilimento; è stato installato un sistema di recupero termico dei fumi provenienti dal post combustore catalitico che garantisce l’integrazione dei sistemi di asciugatura della stampa e la climatizzazione degli ambienti, e moderni sistemi di supervisione riducono al minimo gli scarti per errori di lavorazione durante la fase di stampa e la fase di micro-foratura dei film, è presente anche un efficiente impianto di recupero e distillazione dei solventi provenienti dalla stampa flessografica.
Corapack c’è e farà la sua parte!