Lo scorso ottobre OMET ha ospitato un open house presso l’Innovation Park e gli OMET Headquarters, dove professionisti del settore si sono riuniti per scoprire le ultime proposte per la stampa di imballaggi: l’evento ha dimostrato la leadership continua di OMET nel settore della stampa di imballaggi, offrendo soluzioni innovative, sostenibili e altamente flessibili, pensate per soddisfare le esigenze sempre più diversificate delle aziende di stampa moderne
L’ evento è iniziato con l’introduzione di Marco Calcagni, Sales & Marketing Director di OMET, che ha ricordato, dopo una breve storia di Omet, come l’azienda sia al fianco di tanti grossi gruppi, tra cui CCL, CTI Group, Constantia Flexible, Labelmarkers, Multi-Color, Eurostampa, All4Labels, Huhtamaki e Master press, sottolineando l’importanza di un rapporto di partnership e collaborazione con tutte le aziende, anche le più piccole: l’obiettivo di OMET è aiutarle a crescere nei rispettivi business, assicurandosi così preziose risorse per poter continuare a investire per innovare.
A seguire, Roberto Speri, Area Manager e Product Manager, ha spiegato come i progressi tecnologici di OMET stiano guidando la trasformazione nel settore della stampa, per essere più sostenibili. Ha analizzato nel dettaglio le possibilità offerte dalla Omet Varyflex V4 (EB wet/Wet-UV Wet/Wet- UV Wet/Dry): la macchina si basa su una piattaforma offset con tecnologia a sleeve, e raggiunge la velocità meccanica massima di 400 metri al minuto. La macchina può stampare supporti a più strati grazie a un sistema brevettato che consente di utilizzare materiale triplex e quadruplex con strato di alluminio trattato con EB, il tutto ad alte velocità senza la necessità di laminazione post-stampa. Possibile ovviamente anche la stampa di caratteri braille e di pittogrammi tattili grazie a due barre per gestire configurazioni multiple con allineamento automatico. La macchina è completamente modulare, e può essere configurata in base alle esigenze del lavoro da stampare.
Nell’unità offset troviamo un altro brevetto relativo all’albero fisso della lastra, all’albero del caucciù con movimento circolare e a quello di stampa con movimento lineare. Il calamaio ha settori indipendenti che garantiscono un’elevata precisione dell’inchiostrazione e stabilità; il treno inchiostratore ha 19 cilindri e controllo della temperatura, i rulli bagnatori della forma sono 4 e 3 sono dotati di un particolare sistema di oscillazione anti-effetto fantasma; la bagnatura è costante ma differenziata.
E la conversione da gruppo stampa offset a flexo e/o rotocalco: veloce e facile! Possibile anche la stampa flexo verticale, che si può impostare con varie configurazioni. Il gruppo rotocalco ha un nuovo design e garantisce ottima accessibilità da entrambi i lati, e permette la stampa in bianca e in volta.
Uno dei punti di forza della Varyflex V4 è la rapidità del cambio lavoro che, grazie al sistema Easy Sleeve Format Change, consente di effettuare un intero cambio formato in pochissimo tempo in modo semplice, veloce e soprattutto sicuro. Questo riduce notevolmente i tempi di cambio lavoro e aumenta la flessibilità operativa, rendendola ideale sia per tirature brevi che per quelle lunghe.
Grazie ai sistemi di controllo della tensione avanzati di OMET, la Varyflex V4 ha una qualità di stampa ottimale su supporti diversi, riducendo al minimo gli scarti e garantendo risultati costanti. Il pre-registro automatico e il sistema Vision ha ulteriormente ridotto i tempi di avviamento, portando ogni lavoro al registro perfetto con il minimo sforzo e spreco di materiale.
Speri ha poi sottolineato che la Omet Varyflex V4 garantisce una stampa sostenibile perché ha un basso consumo di energia, l’essiccazione EB non produce VOC, consuma meno inchiostro, produce meno scarti e non utilizza solventi.
Tecnologia EB, inchiostri EB: tutto per una stampa più sostenibile
Brian Sullivan, Vicepresidente Marketing e Vendite di Energy Science Inc., ha evidenziato come la tecnologia Electron Beam (EB) stia diventando la soluzione leader per una stampa eco-sostenibile.
ESI è leader nel trattamento EB con moltissime installazioni di impianti EB su macchine offset a bobina in tutto il mondo.
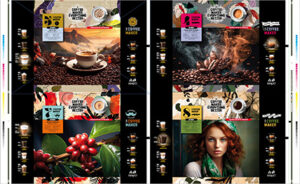
La tecnologia EB prevede un sistema che accelera gli elettroni e li proietta sul supporto (gli elettroni vengono generati facendo passare della corrente elettrica attraverso un filamento di tungsteno e poi accelerati in un campo elettrico applicato), questo fascio provoca cambiamenti molecolari, e la dose e la densità energetica sono modulati a seconda dell’applicazione. I vantaggi sono molti: innanzitutto il consumo di energia è basso, il trattamento è idoneo per imballaggi alimentari, non ci sono odori, non servono fotoiniziatori, la resistenza al calore, ai graffi, all’abrasione e chimica è elevata e il risultato è un supporto brillante.
Norbert Wünsch di Zeller-Gmelin ha ricordato nuovamente i vantaggi degli inchiostri EB e ha sottolineato che l’impiego d questa tecnologia è in aumento. L’azienda offre la gamma Esalux E4 per stampa offset. Thomas Ellinger di Actega ha chiuso il ciclo di interventi con una discussione sugli ultimi aggiornamenti normativi per le vernici UV.
Dimostrazioni sulla Varyflex V4
Dopo le presentazioni, i partecipanti hanno assistito alla dimostrazione dal vivo della Varyflex V4, la macchina da stampa con tecnologia combinata offset/flexo dedicata agli imballaggi flessibili. La macchina, presentata con una larghezza di nastro di 850 mm, ma disponibile anche con larghezze 670 mm e 1080 mm, ha dimostrato la sua versatilità nel gestire una vasta gamma di materiali, come film non supportati, multi-laminati e astucci pieghevoli.
Durante la dimostrazione, la Varyflex V4 ha stampato un imballaggio per caffè su un film PET da 12 micron, utilizzando una combinazione di 4 colori offset EB e un bianco flexo EB. Il processo di stampa ibrida, eseguito a 300 metri al minuto con configurazione Wet-on-Wet, ha evidenziato la capacità della macchina di combinare la qualità offset con la coprenza del bianco flexo, il tutto asciugato con tecnologia EB. Il cambio lavoro rapido, completato in soli 10 minuti, ha mostrato l’efficienza della macchina mentre passava senza sforzo a un supporto in cartone da 350 grammi, producendo una stampa fotografica di alta qualità con verniciature lucide e soft touch.
Durante la dimostrazione, è intervenuto anche Roberto Maiocchi, Sales & Marketing Manager di BST eltromat Italia, partner storico di OMET. Maiocchi ha fornito interessanti approfondimenti sul sistema di controllo qualità della stampa, spiegando come i dispositivi di controllo BST integrati sulle macchine OMET permettano di monitorare la qualità in tempo reale, garantendo risultati eccellenti e costanti anche durante lavori complessi.
La giornata si è poi conclusa con il tour nel reparto produttivo di OMET dove è stato possibile scoprire i processi di produzione avanzati e le tecnologie che sono alla base del successo dell’azienda.