Affidabilità e velocità di stampa non sono più fattori limitanti, a tal punto da guidare lo sviluppo delle macchine da stampa flexo digitali ibride. Per Gallus (Gruppo Heidelberg) è la conferma di un concetto da sempre perseguito. L’azienda afferma che ora, per lo sviluppo di nuove soluzioni ibride, si basa sulle tre fasi che hanno caratterizzato il suo sviluppo digitale.
By Dieter Finna
Guardando indietro al design delle macchine da stampa Gallus, la produzione di etichette e imballaggi in un unico passaggio è nel suo DNA. Ciò non è cambiato nemmeno quando i processi di stampa digitale elettrofotografica e i metodi di produzione con macchine indipendenti si sono fatti strada nel mercato della stampa di etichette.
La base delle attuali soluzioni ibride
Gallus ha introdotto sul mercato un sistema di stampa flessografica digitale ibrido quando è entrato per la prima volta nel campo della stampa digitale, con la Labelfire nel 2016. Negli anni successivi, la macchina ha subito un ulteriore sviluppo significativo ed è ora utilizzato da diversi stampatori ad alte prestazioni, 24/7 in continuo. Le esigenze dei proprietari di marchi nel settore del tabacco hanno influenzato in modo significativo lo sviluppo dei sistemi di macchine. Nel mercato odierno, la Gallus Labelfire viene utilizzata allo stesso modo per etichette, astucci pieghevoli e imballaggi speciali. L’azienda può contare su tre fasi di sviluppo per la progettazione di sistemi di macchine ibride.
Sviluppo graduale della stampa digitale
La prima fase, che Gallus descrive come la fase di innovazione delle soluzioni digitali, prevede la sfida di integrare la stampa inkjet in un sistema di stampa ibrido digitale/flessografico. Il punto di partenza per lo sviluppo è stata l’iniziale mancanza di uniformità delle prestazioni della stampa inkjet, rispetto ai processi convenzionali. Ciò ha reso necessario integrare la migliore tecnologia della testina di stampa nel concetto della macchina. Con la loro integrazione, Gallus è riuscita quindi ad ampliare notevolmente la finestra di processo in cui le testine di stampa inkjet funzionano in modo affidabile.
A causa della mancanza di soluzioni esistenti sul mercato, nel 2019 Heidelberg/Gallus ha deciso di realizzare numerosi sviluppi interni, che hanno preannunciato la stabilizzazione e quindi la seconda fase del suo sistema di stampa flessografica digitale ibrida. L’attenzione si è concentrata sul “Sistema di visione” basato su telecamera per la compensazione degli artefatti e sullo sviluppo associato degli algoritmi necessari per contrastare gli errori rilevati come gli ugelli mancanti e l’irregolarità della densità nei fondi pieni.
Un importante salto di qualità di stampa è stato ottenuto anche abbassando le testine di stampa più vicino al supporto, aumentando significativamente la precisione del getto delle gocce di inchiostro. L’abbassamento delle testine, a sua volta, ha richiesto l’installazione di un sistema di rilevamento automatico della giunzione tramite sensori, al fine di prevedere un aumento della distanza tra le testine di stampa e il supporto con breve preavviso, cioè quando sono state rilevate giunzioni nel nastro, e per proteggere le testine di stampa da eventuali danni. Questa fase è generalmente indicata in Gallus come il periodo in cui l’azienda ha messo in atto passi fondamentali di sviluppo che hanno portato a un funzionamento stabile e continuo dei sistemi di stampa ibrida e hanno assicurato all’azienda una posizione di leadership nell’eliminazione degli errori di processo.
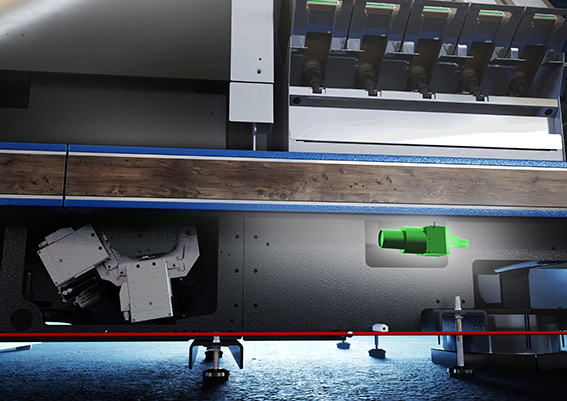
Sostenuto dalla consolidata tecnologia Labelfire, all’inizio della terza fase nel 2022 Gallus si è concentrata su concetti innovativi di “facilità d’uso”. Sviluppi che semplificano la stampa digitale e alleggeriscono gli operatori: un aspetto sempre più importante, soprattutto in un’epoca di carenza di manodopera qualificata. Ciò includeva l’ulteriore sviluppo del “Sistema di visione” in una variante altamente automatizzata con la quale è possibile stampare un grafico di prova tra ogni lavoro e non solo manualmente una volta al giorno, come avviene di solito. Questa soluzione automatizzata fornisce all’operatore un’assistenza rapida quando ci sono “ugelli deboli”, che diventano evidenti solo durante le operazioni quotidiane. La loro eliminazione diretta influisce sulla qualità di stampa attraverso la massima stabilità e coerenza possibile del processo.
Una maggiore facilità d’uso e standardizzazione si ottengono anche pulendo le testine di stampa con un processo di pulizia completamente automatizzato, per il quale l’operatore può inoltre attivare una fase di pulizia a ultrasuoni. In pratica, questa soluzione di progettazione si è dimostrata talmente valida che il contatto fisico con le testine di stampa non è più necessario durante il processo di pulizia e il principio di pulizia si sta rivelando rivoluzionario per la pulizia standardizzata delle testine di stampa.
Anche l’installazione fissa delle barre di stampa e delle testine di stampa contribuisce alla facilità d’uso. Le testine di stampa montate in modo permanente riducono al minimo la necessità di manutenzione e, grazie a questo minore fabbisogno di manutenzione, portano a una disponibilità della macchina notevolmente maggiore e quindi a un aumento della produttività.
In generale, tutte queste soluzioni di progettazione si basano su un elevato grado di automazione con standard definiti che consentono l’integrazione efficiente della stampa digitale nei sistemi di macchine ibride.
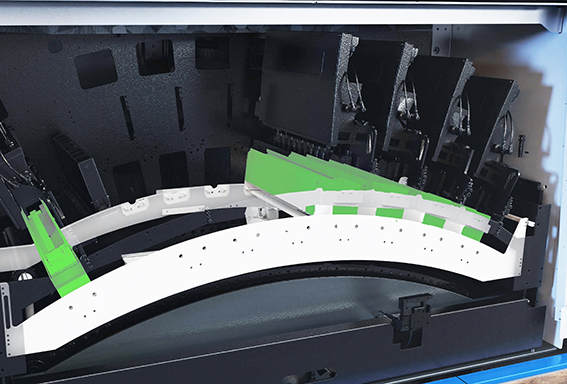
L’influenza della stampa convenzionale sulla tecnologia di stampa ibrida
Ma non è solo la stampa digitale che ha influenzato in termini di prestazioni le soluzioni di stampa ibrida. Parallelamente, si è evoluto anche il tradizionale lato base/portante della macchina e il suo livello di automazione è aumentato a favore della facilità d’uso. Una preimpostazione della macchina da stampa, ad esempio, consente di impostare rapidamente un lavoro recuperando tutti i dati di set-up della macchina da stampa dal file del lavoro. Tra l’altro, la lunghezza del formato e la correzione della lunghezza del formato, i dati relativi al tipo di supporto, spessore e larghezza del nastro e le impostazioni di trasporto del nastro con tensione e allungamento del nastro sono tutti preimpostati.
L’automazione include anche la preimpostazione del registro longitudinale e trasversale, che esegue questa operazione per ogni unità di stampa su ogni lavoro, nonché il controllo e la regolazione permanente del registro durante la tiratura. Questa è una funzione molto comoda che libera l’operatore di stampa da questa operazione di controllo, che altrimenti bisognerebbe eseguire costantemente durante l’intera tiratura.
Con il controllo “web-to-web”, i sensori misurano la distanza tra i segni di registro appositamente progettati e reagiscono in modo molto preciso e rapido alle deviazioni nell’immagine di stampa/registro che possono verificarsi, ad esempio, a causa delle tolleranze del supporto. Poiché la macchina regola automaticamente il registro non appena i segni di registro si trovano nella zona di presa, questa modalità di funzionamento contribuisce in modo significativo ad evitare e quindi a ridurre gli scarti.
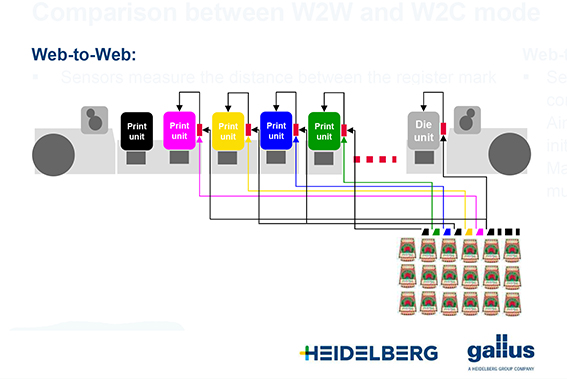
Soluzioni ibride in aumento
Se si guarda all’aumento delle prestazioni nella stampa digitale da un lato e al più alto livello di automazione delle parti di stampa convenzionali dall’altro, si capisce come nascono i sistemi ibridi. Il mercato sta attualmente assistendo a un aumento dello sviluppo di nuove macchine da stampa flexo digitali ibride e di macchine da stampa digitali con finitura in linea e/o unità flexo, anche se vari processi di finitura come serigrafia, stampa a caldo, laminazione digitale e verniciatura digitale continuano ancora in qualche modo a rallentare il processo in linea.
A seconda della struttura dell’ordine, il futuro sta spesso nel processo in linea, soprattutto per tirature medio-lunghe e un livello di finitura medio. In questa situazione, non sorprende che la Gallus One, recentemente presentata come macchina stand-alone, segua anche il DNA ibrido dell’azienda di ingegneria meccanica di San Gallo e abbia le potenzialità per diventare una macchina in linea o una macchina flessografica digitale ibrida.